Explore the fascinating world of interactive 3D printed sculptures! Discover how MIT’s Xstrings and other innovations let art twist, fold, and react, changing how we experience creativity.
Beyond Stillness – When Art Gets Interactive
Imagine stepping into an art gallery, expecting the usual quiet contemplation of static paintings and sculptures. But then, something catches your eye. A piece doesn’t just sit there; it responds. Perhaps a delicate structure gently unfurls like a blooming flower as you approach, or a wall-mounted form ripples with light, mirroring your movement. This isn’t a scene from a futuristic movie; it’s the vibrant, evolving world of interactive art, a realm where technology and creativity collide to reshape our very definition of artistic experience.
At its heart, interactive art is a form of expression that invites—or even requires—the viewer to participate. It marks a significant departure from traditional art forms, where the spectator’s role is often limited to observation and mental interpretation. Instead, interactive art transforms the viewer into an active participant, someone whose presence, touch, or movement becomes integral to the artwork’s completion or purpose. Creation is no longer seen solely as the artist’s solitary act but emerges from a dynamic collaboration, a dialogue between the artist, the artwork, and the audience. Think of it less like gazing at a finished painting and more like engaging in a conversation where your input shapes the outcome.
This concept isn’t entirely novel. Artists have experimented with viewer participation for decades. Consider Marcel Duchamp’s “Rotary Glass Plates” from the 1920s, which required the viewer to activate the machine and stand at a specific distance to perceive an optical illusion. However, the advent of modern technology—particularly computers, sensors, and sophisticated fabrication methods—has dramatically expanded the horizons of interactivity. Early interactive pieces might have relied on simple mechanics or visual tricks, but today’s technology empowers artists to create works that respond in complex, nuanced, and often surprising ways. Sensors can detect motion, heat, proximity, sound, or even meteorological changes, while software and actuators translate these inputs into responses like changing lights, moving parts, or evolving projections. Technology essentially provides the artwork with its own senses and muscles, allowing it to perceive its environment and react dynamically.
This technological infusion is doing more than just adding novelty; it’s facilitating a fundamental reevaluation of what art can be. Traditional art often prioritizes the final, static object, embodying the artist’s singular vision. Interactive art, conversely, often emphasizes the process and the experience. Because the artwork’s outcome or meaning is directly influenced by the viewer’s input, each interaction can produce a unique result, effectively blurring the lines between the creator and the audience. The complex, real-time responsiveness made possible by digital tools wasn’t feasible before the digital age. Consequently, the technology isn’t merely a new tool in the artist’s kit; it’s the engine driving a paradigm shift. The focus moves from the art object to the art system or experience, where the interaction itself generates meaning. How, then, does a technology often associated with rapid prototyping or creating plastic trinkets become a pivotal force in bringing sculptures to life? The answer lies in the versatile and increasingly sophisticated capabilities of 3D printing.
3D Printing: The Artist’s New Magic Toolbox
For centuries, sculptors have worked with materials like stone, wood, metal, and clay, employing techniques such as carving, modeling, casting, and assembling. While these traditional methods have produced masterpieces, they often come with inherent limitations. Creating highly intricate details, complex internal structures, or forms with delicate, interlocking parts can be incredibly time-consuming, technically demanding, and sometimes simply impossible with conventional tools and materials. The properties of the chosen material heavily dictate the achievable forms, and the process can be slow and unforgiving.
Enter 3D printing, also known as additive manufacturing. In its simplest terms, 3D printing builds objects layer by painstaking layer directly from a digital design file. Imagine a high-tech, incredibly precise hot glue gun tracing out a shape, layer by layer, until a three-dimensional object emerges. Several different techniques exist, each with its own strengths. Fused Deposition Modeling (FDM) is perhaps the most common, extruding melted plastic filament much like that glue gun. Stereolithography (SLA) uses ultraviolet light to selectively harden liquid resin, capable of producing very fine details. Selective Laser Sintering (SLS) employs a laser to fuse powdered materials—like plastics or even metals—together, creating strong and durable parts. For artists looking to push boundaries, these technologies offer a powerful new set of capabilities:
- Unprecedented Design Freedom & Complexity: Perhaps the most significant advantage is the ability to create forms previously unimaginable. Artists can design and fabricate incredibly intricate patterns, delicate filigree structures (like Joshua Harker’s lace-like skulls ), complex internal geometries, and organic shapes that would be extraordinarily difficult or impossible to achieve by hand. The digital design process allows for a level of precision and complexity limited more by imagination than physical constraints.
- A Diverse Material Playground: 3D printing liberates artists from the constraints of traditional materials. They can work with a vast and growing palette, including various plastics like PLA and PETG (offering different colors and properties), flexible filaments like TPU (essential for creating bendable parts), high-detail resins, ceramics, metals (stainless steel, bronze, titanium), and even recycled or biodegradable materials. This material diversity allows for exploration of different textures, colors, weights, and functional characteristics—such as the flexibility needed for kinetic or interactive elements.
- Speed, Iteration, and Experimentation: Traditional sculpting can take months. 3D printing drastically reduces production times, allowing artists to transform a digital concept into a physical object much more quickly. This speed facilitates rapid prototyping—the ability to quickly create, test, and refine designs. Artists can experiment with different forms or variations, learn from failures, and iterate on their ideas without the significant time and material investment required by traditional methods. This lower-risk experimentation can foster greater creativity and innovation.
- Seamless Integration of Mechanisms: This is a game-changer for interactive and kinetic art. 3D printing allows artists to design and embed functional components—like joints, gears, channels for wiring, or housings for sensors and actuators—directly into the sculpture during the printing process. This seamless integration simplifies the creation of complex moving parts and responsive systems, making the artwork’s “inner workings” an inherent part of its structure.
- Customization and Scalability: Digital designs are easily modified. Artists can readily adjust the size, shape, or details of a sculpture to create unique, personalized pieces or limited editions. Furthermore, large-format 3D printers now enable the creation of massive sculptures, overcoming traditional size limitations, particularly for public art installations.
The capacity to design and integrate mechanisms directly within the printed object is particularly revolutionary for art that aims to move or interact. It bridges the gap between static form and dynamic behavior. This potential hasn’t gone unnoticed, and researchers at the Massachusetts Institute of Technology (MIT) have developed a particularly ingenious method, called Xstrings, that specifically leverages this capability to create complex, cable-driven motion in a single print.
The shift towards 3D printing signifies more than just adopting new tools; it represents a potential transformation in the artistic creation process itself. While traditional sculpture often relies heavily on direct, hands-on manipulation of physical materials, 3D printing necessitates a significant engagement with the digital realm before the physical object takes shape. Artists must become proficient in digital modeling software, using tools like CAD programs or digital sculpting platforms such as ZBrush or Blender to translate their vision into printable data. The emphasis on rapid prototyping and iteration introduces a design thinking methodology more commonly found in engineering or software development. Furthermore, integrating mechanisms requires at least a basic understanding of mechanical principles, often facilitated by the design software. While traditional craft skills certainly remain valuable, especially for finishing touches or in hybrid approaches combining digital fabrication with manual techniques, a degree of digital fluency—understanding modeling, simulation, and the specific capabilities and constraints of various printing technologies —becomes increasingly vital. This suggests an ongoing evolution in artistic practice and perhaps even in art education, where digital literacy becomes as fundamental as drawing or sculpting skills once were.
3D printing approach strings together dynamic objects for you
Unraveling Xstrings: MIT’s Breakthrough in Motion
Imagine trying to build a complex marionette, painstakingly threading dozens of tiny strings through minuscule holes and tying knots in just the right places. It’s a fiddly, time-consuming process demanding immense patience and precision. Now, imagine if you could simply 3D print that marionette with all its strings perfectly embedded, ready to dance the moment it comes off the printer. That’s the core idea behind Xstrings, an innovative system developed by researchers at MIT’s renowned Computer Science and Artificial Intelligence Laboratory (CSAIL). It’s presented as an elegant solution to the challenge of creating objects with intricate, cable-driven movement without the laborious manual assembly typically required.
The magic of Xstrings lies in its “print-in-place” approach to cable integration. It utilizes a specific type of 3D printer known as a dual-material Fused Deposition Modeling (FDM) printer. This allows the machine to print using two different materials simultaneously. Xstrings leverages this capability to construct the main body of the object using one material (often a standard rigid plastic) while concurrently embedding thin, strong, flexible “strings” or cables made of a second material directly within the structure, all in a single, uninterrupted printing process. This eliminates the need for the tedious post-print steps of manually threading cables through channels and securing them.
How the Magic Happens: Materials and Process
The system typically employs readily available 3D printing materials. The main structure is often printed using Polylactic Acid (PLA), a common and relatively rigid plastic, while the embedded cables are made from a material chosen for its strength and flexibility, such as Nylon (specifically Nylon 66 was found suitable after testing). Crucially, using two different materials with distinct melting points prevents the cable from fusing to the surrounding structure during the printing process, ensuring it can slide freely later.
The FDM printer meticulously builds the object layer by layer. When it reaches a point where a cable needs to be integrated, it switches materials, lays down a segment of the flexible Nylon cable horizontally, and then switches back to the structural material (PLA) to build around it, encasing the cable within the object’s geometry. Achieving this successfully requires careful optimization of printing parameters. The MIT researchers found that specific settings, such as a printing temperature around 260°C and a reduced printing speed (10-20 millimeters per second), were ideal for producing strong, functional cables without breakage or unwanted fusion. They also employed techniques like adjusting material spacing in the first cable layer and reducing extrusion rates to further prevent fusion and ensure cable straightness.
The Xstrings system defines three key components for how these cables are integrated and function :
- Anchor Points: These are the endpoints where the cable is securely fixed within the structure. The system automatically generates a T-shaped anchor at the cable end, which is embedded in the surrounding material, providing a strong mechanical hold without relying on thermal bonding.
- Threaded Points: These are the channels or holes within the printed object through which the cable passes and slides when actuated. The design tool automatically creates these channels with a slight offset (e.g., 0.5mm) around the cable’s path to minimize friction and ensure smooth movement.
- Exposed Points: These are the ends of the cables left accessible outside the main structure. This is where the user (or potentially a motor or other actuator) applies force—typically by pulling—to operate the mechanism and induce movement. The design tool allows customization of these points into shapes like rings for manual pulling or spools for connection to servos.
The Four Fundamental Moves
Xstrings enables the creation of four basic types of cable-driven motion, referred to as “motion primitives.” These primitives act as building blocks for more complex movements :
Motion Primitive | Simple Description | Analogy | How it Works (Simplified) |
---|---|---|---|
Bend | Curling motion along a path | Like curling a finger | Multiple joints allow rotation; pulling cable causes bend. |
Coil | Tightening into a spiral shape | Like a spring coiling | Builds on ‘Bend’ but angles segments for helical motion. |
Screw | Twisting and shortening along axis | Like turning a screw | Helical structure with joints converts pull to twist/compress. |
Compress | Shortening along a straight line | Like an accordion folding | Cable pulls segments together along a linear track. |
These primitives can be combined in series (like multiple bends to make a snake-like curve) or in parallel (like multiple bending fingers on a robotic hand) to create a wide array of sophisticated movements.
Making Design Accessible: The Software Tool
Recognizing that designing such complex mechanisms could be daunting, the Xstrings system includes a user-friendly design tool. Built using common design software platforms (Rhinoceros 8 and Grasshopper) , this tool allows users, even those without deep engineering expertise, to easily embed these cable-driven mechanisms. Users can import a 3D model, select the desired motion primitives, define parameters like the angle of movement or number of segments using simple sliders, specify how and where the cables should be anchored and exposed, and simulate the resulting motion to preview the behavior before committing to printing. The tool then prepares the necessary files for the dual-material 3D printer, outputting separate files for the main structure and the cable layers with recommended settings.
The Xstrings Advantage
The primary benefit of Xstrings is a dramatic reduction in production time and effort. By automating the intricate process of cable embedding, the researchers report reducing the total time required by about 40% compared to manual assembly methods. This efficiency opens the door for broader experimentation and application. As lead author Jiaji Li stated, “Our innovative method can help anyone design and fabricate cable-driven products with a desktop bi-material 3D printer,” empowering creators to “bring a variety of ideas to life”. Durability testing also showed promising results, with the embedded Nylon cables reportedly withstanding over 60,000 pull cycles before breaking, demonstrating the robustness of the print-in-place approach.
This method represents a significant advancement towards achieving “functional” 3D printing directly from the machine. Traditional additive manufacturing often produces static components that need subsequent assembly with motors, actuators, or linkages to achieve motion. Xstrings, however, integrates the core actuation mechanism—the cable system—during the print itself. The result is a single printed object possessing inherent potential for specific, complex movements, activated simply by pulling the embedded cables. The accompanying design software further abstracts the mechanical complexity, allowing users to focus on the desired behavior rather than intricate mechanism design. In essence, Xstrings moves beyond printing just form to printing kinetic function, making the creation of dynamic objects more integrated, accessible, and efficient. This capability could pave the way for even more complex print-in-place robotic systems and interactive devices in the future. But words and theory only go so far; the true potential shines through in the objects created.
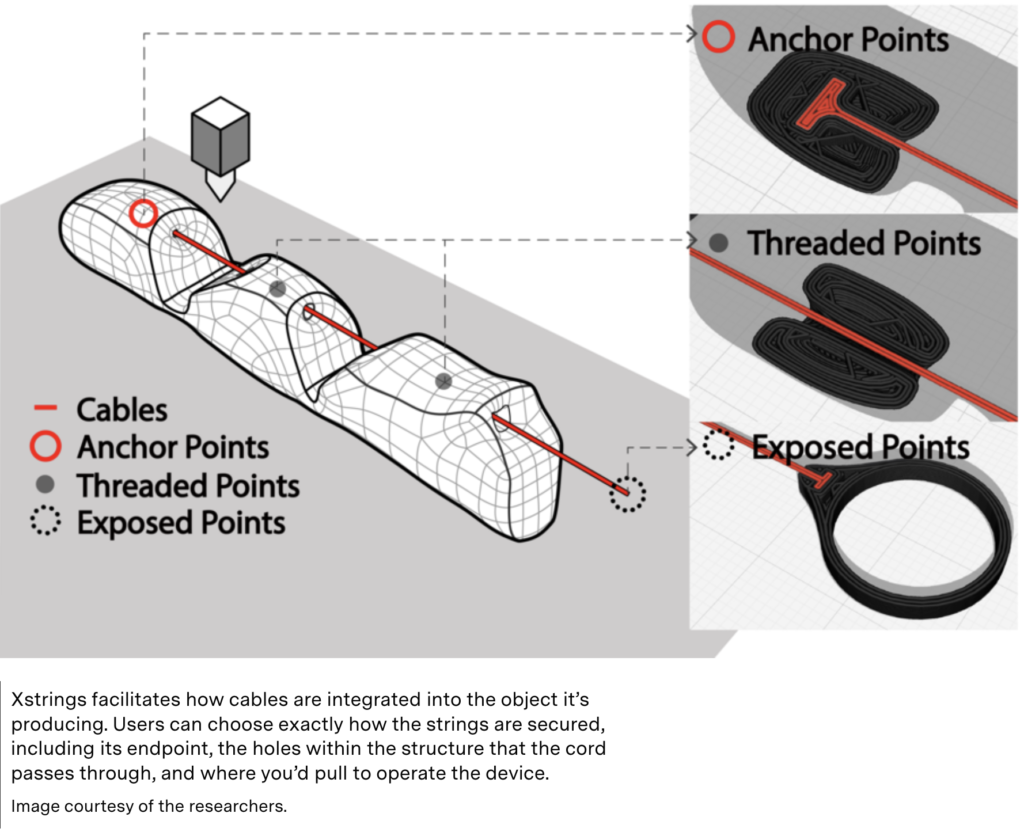
Gallery of Motion: See Xstrings Come Alive!
The true excitement of a technology like Xstrings lies not just in the cleverness of the engineering but in the tangible, moving creations it enables. These aren’t just abstract lab experiments; they are demonstrations of potential, hinting at future applications ranging from interactive art installations that engage gallery visitors in new ways to functional robotic components that mimic the efficiency of biological systems. Let’s step into a virtual gallery and look at some of the remarkable prototypes brought to life by MIT researchers using the Xstrings method:
- The Scuttling Lizard: Picture a small robot, its body segmented and printed in a vibrant red plastic. Embedded within, following paths laid out by the Xstrings design tool, are the crucial Nylon cables. When these hidden “tendons” are pulled, perhaps by tiny motors or even by hand, the lizard springs to life. Its legs scrabble, its body articulates with a surprisingly lifelike wiggle, allowing it to walk across a surface. This example vividly demonstrates the potential for Xstrings in creating bio-inspired robots, mimicking the movements of living creatures through purely mechanical, printed means.
- The Blooming Peacock Sculpture: Imagine a striking piece of wall art printed in a rich purple hue. At rest, it might appear as a compact, geometric form. But activate the embedded cables, and the sculpture undergoes a transformation. Its segments gracefully fan outwards, expanding and unfolding in a motion reminiscent of a peacock displaying its stunning tail feathers, only to contract back again when the tension is released. This prototype highlights the immense artistic potential of Xstrings, enabling the creation of dynamic, interactive sculptures with unique and captivating geometries that respond to input.
- The Grasping Tentacle: Envision a long, segmented appendage, perhaps printed in white, resembling an octopus tentacle or a robotic arm. This prototype likely utilizes the “coil” or “bend” primitives. Pulling the integrated cables causes the tentacle to curl inwards with a smooth, fluid motion. Researchers demonstrated its ability to wrap around and gently grasp objects like a pencil, showcasing its potential for delicate manipulation tasks and mimicking the flexible movements found in nature. The paper specifically mentions a multi-directional tentacle prototype, 352mm long, using three cables to control bending left, coiling at the tip, and bending right, enabling complex maneuvers.
- The Functional Gripping Claw: Think of a mechanical hand or claw, also printed with its actuating cables already inside. This example likely employs multiple cables working in parallel – one for each “finger” or segment. Actuating these cables in concert causes the individual digits to curl inwards simultaneously, forming a fist capable of securely gripping objects. This demonstrates the ability to create more complex, coordinated movements suitable for functional robotics and prosthetic applications.
These diverse examples effectively showcase the versatility of the Xstrings system. They illustrate how the four fundamental motion primitives—bend, coil, screw, and compress—can be implemented and combined to achieve a wide range of movements, from the bio-mimetic scuttling of the lizard to the artistic flourish of the peacock and the functional grasp of the tentacle and claw. They underscore the power of integrating movement directly into the 3D printing process, transforming static plastic into dynamic, responsive objects.
The deliberate variety in these prototypes—spanning biomimicry, art, and robotics —strongly suggests that the researchers conceived Xstrings not merely as a tool for a single niche but as a versatile platform technology. By demonstrating its applicability across these different domains, they aim to inspire broader adoption and further innovation, encouraging artists, designers, and engineers alike to explore the possibilities of print-in-place kinetic structures. While MIT’s Xstrings represents a significant leap forward, it builds upon and contributes to a wider, exciting trend: artists and designers globally are increasingly turning to 3D printing as a means to imbue their creations with motion, interactivity, and life.
The Kinetic Canvas: More Artists Making Moves with 3D Printing
While the Xstrings method offers a fascinating glimpse into the future of integrated kinetic design, it’s part of a broader artistic movement embracing digital fabrication to create sculptures that move, react, and engage audiences in unprecedented ways. Artists and design studios around the world have been harnessing the unique capabilities of 3D printing to explore the realms of kinetic (moving) and interactive art, each bringing their own vision and technical approach. Let’s explore a few prominent examples:
Case Study 1: Nervous System – Weaving Flexibility with Code (Kinematics)
The design studio Nervous System, founded by Jessica Rosenkrantz and Jesse Louis-Rosenberg, has gained renown for its nature-inspired designs generated through computational processes. Their “Kinematics” project stands out as a pioneering example of using 3D printing to create flexible, wearable structures that behave like fabric despite being made from interconnected rigid components. The core idea involves designing complex assemblies of tiny, interlocking triangular panels connected by hinges. These structures are 3D printed using Selective Laser Sintering (SLS) in nylon plastic, but with a crucial twist: they are printed in a highly compressed, folded state generated through physics simulations. Once removed from the printer, the object can be unfolded into its final, flexible form—a dress, a bodice, or jewelry—requiring no manual assembly. This process is often cited as an example of “4D printing,” where the fourth dimension, time, involves the object transforming its shape after the initial 3D print is complete.
The journey to create pieces like the Kinematics Bodice and Dress wasn’t straightforward, offering a compelling story of artistic and technical perseverance. The team faced significant challenges, particularly with achieving the necessary precision for the tiny hinges using SLS printing. The heat from the laser could easily fuse parts that were too close together (within ~0.5mm), potentially rendering the entire piece solid and inflexible. This demanded extreme accuracy in both the design and the simulation used to fold the digital model. The physics simulations themselves proved complex, involving thousands of interconnected parts and constraints. Initial attempts using the Bullet Physics engine encountered stability issues, while the Open Dynamics Engine (ODE) offered improvements but still struggled with the complexity of larger designs. Achieving sufficient compression for printing while maintaining hinge integrity required developing sophisticated folding strategies, mimicking how one might fold actual clothing, and introducing error-correction procedures into their workflow. They printed prototypes, like the bodice composed of 1,320 unique pieces, to test everything from the body scan accuracy and fit to the wearability and the success of the folding simulation before committing to a full dress. Their work beautifully illustrates how 3D printing, combined with advanced simulation, can create intricate, large-scale kinetic forms that adapt to the human body. While primarily kinetic and wearable, the ability to customize designs based on individual 3D body scans adds a layer of personalized interaction.
Case Study 2: John Edmark – Mathematical Motion and Playful Interaction
Artist and designer John Edmark finds inspiration in the mathematical patterns inherent in nature, particularly the Fibonacci sequence and the golden ratio (phi). He uses 3D printing with remarkable precision to create kinetic sculptures that bring these mathematical concepts to life. His widely recognized “Blooms” are intricate sculptures designed to animate when spun under a strobe light. Each petal-like element is placed at an angle of 137.5º (the golden angle) relative to the previous one, mirroring the spiral arrangements found in sunflowers and pinecones. When the rotation speed is synchronized with the strobe flash rate, the sculptures appear to bloom and move in mesmerizing, organic ways—an effect entirely dependent on the geometric accuracy achievable through 3D printing.
Beyond the strobe-animated pieces, Edmark creates what he calls “playable art”—kinetic sculptures designed for direct interaction. Works like the “Helicone,” a wooden structure that transforms from a helix to a pinecone shape with a simple twist, or the “Nautilus Column,” which unfurls elegantly, invite viewers to touch, manipulate, and discover the hidden movements embedded in their clever designs. While often fabricated using laser cutting, these pieces share the principle of using precise digital fabrication to enable surprising kinetic behaviors through thoughtful design and viewer interaction.
Case Study 3: ART+COM Studios (Joachim Sauter) – Orchestrating Large-Scale Kinetic Experiences
The late Joachim Sauter, co-founder of the German design studio ART+COM, was a pioneer in using technology to create large-scale, immersive, and often kinetic installations. Their work often operates at an architectural scale, transforming spaces through choreographed movement and light. A prime example is the “Kinetic Sculpture” created for the BMW Museum in Munich. This installation features 714 polished metal spheres suspended individually from the ceiling by thin wires connected to computer-controlled motors. Over a seven-minute cycle, these spheres move with incredible precision, transitioning from apparent chaos into fluidly morphing shapes that outline the forms of iconic BMW car designs. The effect is a mesmerizing “mechatronic narrative” about the process of design itself.
Another stunning example is “Kinetic Rain” in Singapore’s Changi Airport. Here, hundreds of bronze-coated “raindrops” rise and fall on individually controlled wires, forming undulating surfaces, abstract shapes, and even the silhouette of an airplane in a captivating aerial ballet. While these large installations involve complex mechatronics and may not be entirely 3D printed themselves, their creation relies heavily on digital design, simulation, and often digitally fabricated components or jigs for precision assembly. ART+COM’s philosophy emphasizes creating an experience where the underlying technology becomes invisible, allowing the audience to be captivated by the poetic movement and the story being told.
These examples, alongside others like Theo Jansen’s wind-powered Strandbeests (which have 3D printed counterparts ), Ryan Buyssons’ motion-activated kinetic works, or the mesmerizing wall art by creators like Dr. Moon, demonstrate the incredible diversity emerging at the intersection of 3D printing and kinetic/interactive art. The technology isn’t imposing a single style or scale; rather, it’s acting as a versatile enabling platform. Whether it’s the intricate, wearable forms of Nervous System using SLS, the mathematically precise animations of Edmark, the grand architectural gestures of ART+COM leveraging digital control, or accessible FDM creations, 3D printing provides a flexible foundation adaptable to a vast spectrum of artistic visions and interaction modalities. This raises the question: What specific advantages make 3D printing such a powerful catalyst for this dynamic evolution in art?
Why It Matters: The Power of 3D Printing for Interactive Art
The burgeoning field of interactive and kinetic sculpture owes much of its current momentum to the unique capabilities offered by 3D printing. While artists have long dreamed of creating dynamic works, the practical challenges of fabricating complex moving parts and integrating responsive systems often presented significant hurdles. Additive manufacturing provides a suite of tools that directly address these challenges, making the creation of art that moves and reacts more feasible and accessible than ever before. Let’s revisit the key advantages, focusing specifically on their impact on interactive art:
- Complexity Tailored for Motion: Interactive art often requires intricate mechanisms—joints that allow bending, gears that transfer motion, channels that guide cables or wires, or precisely shaped components that interact in specific ways. 3D printing excels at producing such complex geometries, allowing artists to design and fabricate bespoke mechanical elements tailored to the exact movement or interaction they envision. This capability moves beyond aesthetics to enable core functionality.
- Seamless Integration of “Smarts”: Perhaps the most crucial advantage is the ability to embed the components needed for interactivity—sensors, wires, actuators (like the cables in Xstrings), light sources, or even microcontrollers—directly within the structure of the artwork during the printing process. This integration avoids cumbersome external attachments, allowing for cleaner aesthetics and more robust designs where the technology is an intrinsic part of the art, not just an add-on.
- Material Diversity for Dynamic Function: Movement and interaction place specific demands on materials. Parts might need to be flexible yet durable, lightweight yet strong, or possess specific frictional properties. 3D printing offers a wide range of materials, from rigid plastics and metals to highly flexible elastomers (like TPU) and specialized resins. This allows artists to select materials precisely suited to the functional requirements of their kinetic or interactive designs, ensuring the piece can move and respond as intended, repeatedly and reliably.
- Rapid Prototyping for Interactive Behavior: Designing interactivity is inherently iterative. How a piece feels when touched, how it responds to movement, or how gracefully it performs a kinetic sequence often requires physical testing and refinement. 3D printing’s speed enables rapid prototyping, allowing artists to quickly print, test, and modify the dynamic aspects of their work. This trial-and-error process is vital for fine-tuning the interactive experience and ensuring the desired behavior is achieved.
- Customization for Unique Interactions: Interactive art often involves tailoring the experience. 3D printing makes it relatively easy to customize components for specific types of interaction, user inputs, or even individual users (as seen in Nervous System’s body-scanned wearables). This allows for highly personalized or site-specific interactive artworks.
These advantages don’t exist in isolation; they work synergistically. The ability to design complex forms allows for intricate mechanisms, which can be seamlessly integrated using diverse materials chosen for their function, all while rapid prototyping enables the refinement of the resulting dynamic behavior. 3D printing effectively acts as a powerful translator, bridging the gap between an artist’s digital design of an interactive concept and the physical object capable of performing that interaction in the real world.
This technological empowerment potentially shifts the artist’s focus. Historically, the sheer engineering challenge of making something move reliably could consume a vast amount of an artist’s time and resources. By simplifying or automating aspects of mechanism design and fabrication and by enabling faster iteration on behavior, 3D printing may lower the technical barrier to entry. This could free up artists to concentrate more on the conceptual underpinnings of their work: the nature of the interaction they want to create, the narrative the movement tells, the quality of the relationship fostered with the viewer, and the overall aesthetic and emotional impact of the dynamic experience. The result could be interactive art that is not only technically impressive but also conceptually richer and more deeply engaging. This technological shift isn’t just changing how art is made; it’s fundamentally altering what art can be and transforming the audience’s relationship with it.
Redefining Art: You’re Part of the Masterpiece Now
The rise of interactive sculptures, propelled by technologies like 3D printing, is doing more than just adding movement to the gallery space; it’s fundamentally reshaping the relationship between the artwork, the artist, and the audience. Two major shifts are underway, challenging centuries-old assumptions about what art is and how we experience it.
Shift 1: From Static Object to Dynamic Experience
Traditional sculpture, for the most part, presents itself as a fixed, unchanging object occupying space. Its meaning might evolve through interpretation, but the physical form remains constant. Interactive and kinetic sculptures, however, exist in time as much as in space. They are often processes, events, or performances that unfold, change, and evolve, frequently in direct response to their environment or the people within it. The artwork is not merely the physical object itself but encompasses its behavior, its transformations, and the experience it generates. These sculptures can almost seem to possess agency, exhibiting behaviors—opening, closing, tracking, responding—that give them a life-like quality, moving beyond inert matter into the realm of dynamic systems.
Shift 2: From Passive Viewer to Active Participant
This is perhaps the most profound transformation. In the traditional model, the viewer is primarily an observer, contemplating the artwork from a respectful distance. Interactive art dismantles this separation. The viewer is drawn into the piece, becoming an essential catalyst or collaborator. Their physical presence might trigger a response, their touch might initiate a change, their movement might be mirrored or translated by the artwork, or their data—like the heartbeats powering Rafael Lozano-Hemmer’s “Pulse Room” —might become the artwork’s very pulse.
This active role transforms the viewing experience into a “dialogue”, a “collaboration”, or even a form of “co-creation”. The audience is no longer just looking at the art; they are interacting with it, influencing its state and, potentially, its meaning. This involvement can foster a much deeper sense of connection and engagement. Audience reactions to such works often involve a sense of wonder, curiosity, and surprise. Online comments on kinetic art projects frequently express admiration for both the creativity and the underlying engineering, indicating an appreciation for the fusion of disciplines. Furthermore, the shared experience of interacting with a piece can cultivate a sense of community and connection among viewers, turning the art space into a social environment. By allowing visitors to physically engage, sometimes even playfully, interactive art can make the art experience feel less intimidating and more accessible, potentially attracting audiences who might feel alienated by more traditional, hands-off gallery settings. The gallery becomes a space not just for quiet contemplation but for active discovery and shared experience.
This shift also subtly reframes the artist’s role. While still the originator, the artist becomes less a sole creator of a finished object and more a designer of systems, experiences, or situations that invite and structure audience participation. The focus expands from crafting form to orchestrating behavior and interaction.
The move towards participation and experience in art, significantly enabled by the fabrication possibilities of 3D printing, doesn’t occur in a vacuum. It mirrors broader trends in contemporary society that favor personalization, co-creation, and experiential consumption over passive reception. We see this in interactive entertainment, customizable products, and the rise of the “experience economy.” Interactive art taps directly into this cultural current by empowering the viewer as an active agent. 3D printing provides the crucial link, enabling the creation of the complex, often bespoke hardware needed for these engaging interactions. This alignment suggests that interactive art, fueled by digital fabrication, has the potential to move beyond niche art-world contexts and find greater relevance and application in public spaces, museums, educational settings, and even commercial environments, making art a more integrated and resonant part of contemporary life. This transformation, however, is far from over. The fusion of digital fabrication, interactivity, and ever-smarter materials points towards an even more dynamic future.
What’s Next? The Future Is Smart, Responsive, and Printed
The journey from static sculptures to interactive installations powered by 3D printing is already remarkable, but it represents just the beginning of a fascinating trajectory. The current forms of interaction—responding to touch, presence, or simple motion—are merely scratching the surface of what might be possible. Future artworks could exhibit far more complex and nuanced behaviors, reacting to a richer tapestry of inputs:
- Environmental Attunement: Imagine sculptures that change color with the temperature, shift form based on ambient light levels, or subtly alter their configuration in response to air quality data (like CO2 levels).
- Sensory Dialogue: Works could respond dynamically to sound, music, or even spoken voice commands.
- Biometric Feedback Loops: Moving beyond simple triggers like heart rate, future pieces might engage with more complex biometric data, perhaps responding to brainwave patterns or stress levels detected by wearable sensors.
- Data Embodiment: Artworks could become physical visualizations of real-time data streams, morphing in response to social media trends, financial market fluctuations, or news headlines.
Achieving these sophisticated levels of responsiveness likely involves moving beyond purely mechanical systems like Xstrings towards the integration of “smart materials” and the concept of 4D printing.
Smart Materials and the Dawn of 4D Printing
Smart materials are substances engineered to change their shape, properties (like stiffness or color), or even perform functions in response to specific external stimuli—such as heat, light, water, electricity, magnetism, or pH changes. Think of materials with a built-in “memory” or responsiveness.
4D printing essentially takes 3D printing and adds the dimension of Time. It involves using 3D printing techniques to fabricate objects from these smart materials. The printed object isn’t static; it’s programmed to transform itself after printing when exposed to the appropriate stimulus. Examples include structures that self-fold into a predetermined shape when placed in water (using responsive hydrogels ), materials that return to an original shape when heated (shape-memory polymers ), or components that bend or twist when exposed to light or magnetic fields. Nervous System’s Kinematics project, with its garments printed flat and designed to unfold, can be seen as an early manifestation of this concept.
Beyond the Gallery: Future Applications
The convergence of advanced digital fabrication, smart materials, and kinetic design opens up possibilities extending far beyond the art world:
- Responsive Architecture and Environments: Imagine building facades with 4D printed elements that automatically adjust to provide shade based on the sun’s position or ventilation systems that open and close in response to temperature or occupancy, potentially reducing energy consumption. Buildings could become more adaptive and energy-efficient.
- Adaptive Fashion and Wearables: Clothing could dynamically change its form, fit, insulation, or even aesthetic appearance based on the wearer’s needs or environmental conditions. MIT Media Lab’s “Kino” project, exploring tiny robots that move on clothing to change its shape or pattern, hints at this direction.
- Soft Robotics and Advanced Bionics: Creating robots with more fluid, lifelike movements, potentially integrating sensing and actuation directly into their printed structure, becomes more feasible. This could lead to better prosthetic limbs, more dexterous robotic grippers, or robots capable of navigating complex environments. The Xstrings team explicitly noted this potential.
- Revolutionary Medical Devices: 4D printing could enable the creation of smart medical implants that deploy or change shape inside the body upon reaching a target location, customized drug delivery systems that release medication in response to specific physiological cues, or tissue engineering scaffolds that adapt as tissue grows.
- Space Exploration and Manufacturing: The ability to print complex, functional structures that can self-assemble or deploy on demand is highly attractive for space missions where launch volume and mass are critical constraints. The Xstrings team suggested their technology could one day enable the rapid, one-step creation of robots in space stations or on other planets. Research groups like MIT Media Lab’s Space Enabled group explore related concepts of applying space technology for societal benefit.
This dynamic future is actively being researched in labs worldwide. Institutions like the MIT Media Lab host numerous projects investigating digital fabrication, tangible media, responsive environments, smart materials, kinetic structures, and computational design, constantly pushing the boundaries of what’s possible.
The progression from static 3D prints to interactive systems like Xstrings and further towards autonomous transformation via 4D printing and smart materials suggests a fascinating evolution. We are moving from creating inert forms to fabricating objects with embedded behaviors and inherent responsiveness. These creations act less like traditional artifacts and more like simple machines or even rudimentary artificial organisms that react to their surroundings. This technological trajectory challenges our fundamental classifications of manufactured objects versus dynamic systems. It points towards a future where materials themselves might possess a form of intelligence and agency, blurring the lines between object, machine, and perhaps even life, with profound implications for fields ranging from architecture and medicine to art and design.
Art That Breathes, Moves, and Connects,
We’ve journeyed from the stillness of traditional sculpture to a vibrant world where art moves, reacts, and invites us to become part of the creation. This transformation is being significantly accelerated by the remarkable capabilities of 3D printing, a technology that offers artists unprecedented freedom in form, material, and complexity. Innovations like MIT’s Xstrings method, which allows intricate, cable-driven mechanisms to be printed directly into objects, exemplify this potential, drastically simplifying the creation of dynamic structures and reducing production time.
Pioneering artists and designers, from Nervous System’s computationally crafted wearables to John Edmark’s mathematically inspired kinetic toys and ART+COM’s large-scale mechatronic narratives, are harnessing these tools to explore new aesthetic territories. They are creating works that challenge the viewer’s role, shifting them from passive observers to active participants in a dialogue with the artwork. This interactivity fosters deeper engagement, breaks down traditional barriers to art appreciation, and turns the experience into one of discovery and connection.
The fusion of art and technology, particularly through digital fabrication, is doing more than just providing new techniques; it’s expanding the very language of artistic expression. It allows for the creation of art that is not static but dynamic, not just observed but experienced, not just contemplated but interacted with. Looking ahead, the integration of smart materials and 4D printing promises even more sophisticated responsiveness, blurring the lines between inert objects and dynamic systems, with potential applications reaching far beyond the gallery walls into architecture, medicine, robotics, and beyond.
This evolution represents an exciting chapter in the history of creativity. It’s a future where the boundary between the physical and digital continues to dissolve, where materials themselves might gain a semblance of life, and where art has the potential to connect with us in more profound and surprising ways. The next time you encounter a sculpture, look closely – it might just be waiting for you to bring it to life. The future of art is moving, and it invites us all to move with it.