3D printing, also known as additive manufacturing, is revolutionizing how we create products, enabling the construction of intricate structures layer by layer directly from digital models. From medical devices to aerospace components, this technology has transformed design and manufacturing, combining precision, efficiency, and customization. This review explores the key processes, materials, and applications of 3D printing, highlighting its role in the Industry 4.0 revolution and providing insights into its current capabilities and future potential.
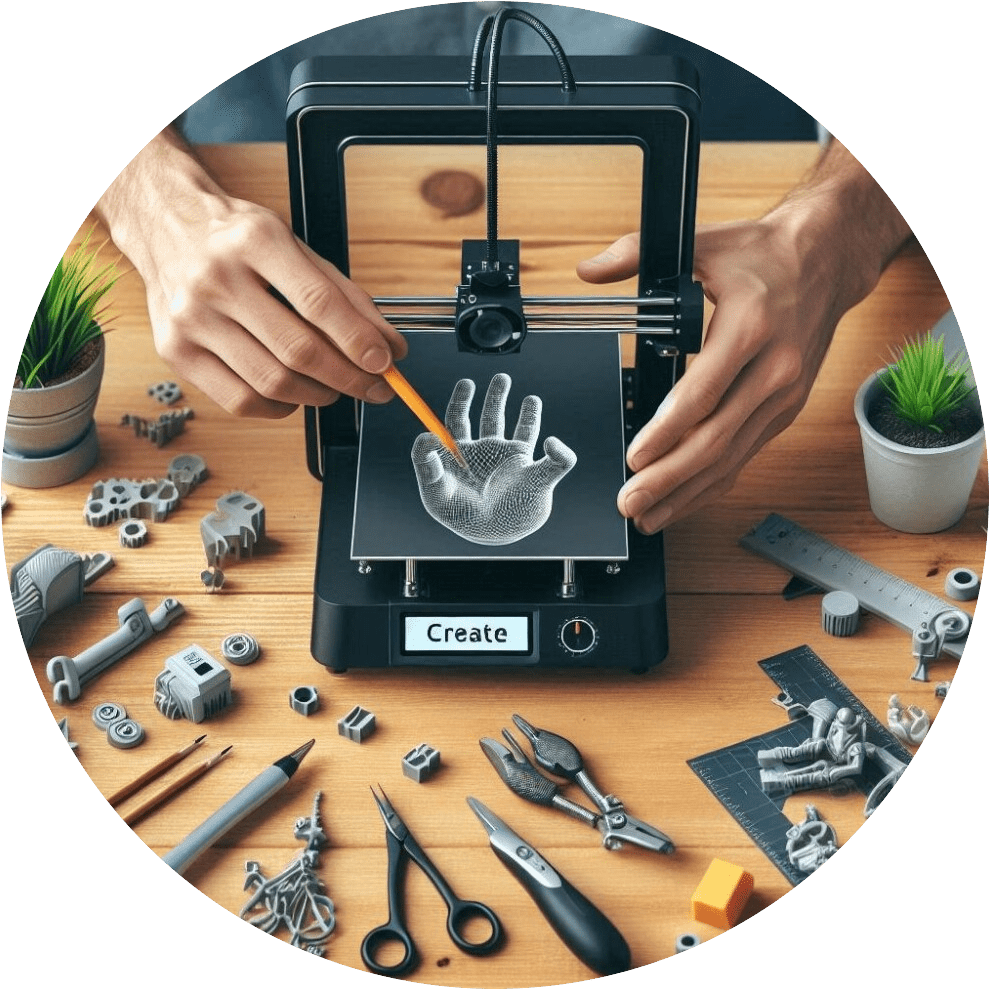
What if the next car part, surgical implant, or even a custom-fit sneaker could be printed layer by layer from a digital file? Welcome to the transformative world of 3D printing, a technology that is redefining manufacturing by overcoming traditional barriers. Unlike conventional methods, which cut or mold material, 3D printing “builds” objects from the ground up by adding material exactly where needed. This flexibility has unlocked endless possibilities, from prototyping tools to creating complex structures like artificial organs and aerospace components.
Since its invention in the 1980s, 3D printing has evolved rapidly. Once limited to prototypes, it now powers industries like healthcare, automotive, construction, and even food production. Understanding the basics of 3D printing processes, materials, and applications is key to appreciating its transformative potential.
1. Types of 3D Printing Processes
3D printing comprises several unique methods, each suited to specific applications. These processes differ in how layers are created, the materials they use, and the final quality of the printed object.
Quick Overview: Common 3D Printing Processes
Process | How It Works | Best For |
---|---|---|
Stereolithography (SL) | UV light cures liquid resin layer by layer. | Smooth, high-detail parts (e.g., dental molds). |
Fused Deposition Modeling (FDM) | Heated plastic filament is extruded layer by layer. | Prototyping, affordable applications. |
Powder Bed Fusion (PBF) | Powder is selectively fused with a laser or electron beam. | Strong, precise parts (e.g., aerospace). |
Binder Jetting (BJ) | Liquid binder “glues” powder layers together. | Molds, colorful prototypes, food items. |
Direct Energy Deposition (DED) | Material is melted and deposited directly onto an existing surface. | Repairing metal tools or machinery. |
Laminated Object Manufacturing (LOM) | Sheets of material are cut and stacked layer by layer. | Large, inexpensive prototypes. |
Let’s explore these processes in greater detail.
1.1. Stereolithography (SL)
Stereolithography is one of the oldest and most precise 3D printing techniques. It uses a liquid resin that hardens when exposed to ultraviolet (UV) light. A laser carefully draws each layer, creating highly detailed parts with smooth surfaces.
- Strengths: Ideal for intricate designs, dental molds, and jewelry.
- Limitations: Resins are often brittle and unsuitable for heavy-load applications.
1.2. Fused Deposition Modeling (FDM)
FDM is the most common and beginner-friendly 3D printing method. It works by melting a plastic filament and extruding it layer by layer to create the object.
- Strengths: Affordable, easy to use, great for prototyping.
- Limitations: Surface finish can be rough, and fine details are harder to achieve.
1.3. Powder Bed Fusion (PBF)
In PBF, a thin layer of powdered material (e.g., metal or plastic) is spread, and a laser or electron beam selectively melts areas to form a solid layer.
- Strengths: Produces strong, precise parts ideal for aerospace and medical applications.
- Limitations: High equipment costs and slower speeds compared to FDM.
1.4. Binder Jetting (BJ)
Binder Jetting spreads a layer of powder and uses a liquid binder to “glue” the particles together.
- Strengths: Faster than many other methods, supports colorful prototypes, and even edible creations like chocolate sculptures.
- Limitations: Final parts often need additional processing for strength.
1.5. Direct Energy Deposition (DED)
DED deposits material (like metal powder or wire) directly onto a surface while simultaneously melting it.
- Strengths: Excellent for repairing or adding to existing parts, such as tools or machinery.
- Limitations: Limited to specific applications like part repair or enhancement.
1.6. Laminated Object Manufacturing (LOM)
LOM stacks and bonds sheets of material, such as paper or metal, layer by layer. A laser or blade cuts each sheet to shape.
- Strengths: Affordable and quick for large prototypes.
- Limitations: Lower precision and weaker mechanical properties compared to other methods.
2. Materials Used in 3D Printing
The success of 3D printing depends heavily on the material used. The choice of material influences the strength, flexibility, and final appearance of the printed object.
Quick Overview: Common 3D Printing Materials
Material | Used In | Key Properties | Applications |
---|---|---|---|
PLA (Polylactic Acid) | FDM | Biodegradable, easy to use, affordable. | Prototyping, decorative items. |
ABS (Acrylonitrile Butadiene Styrene) | FDM | Strong, heat-resistant. | Automotive parts, appliance casings. |
Resins | SL | Smooth finishes, high precision. | Dental molds, jewelry, prototypes. |
Metal Powders | PBF, DED | High strength, durability. | Aerospace, medical implants. |
Ceramics | SLS, BJ | Heat-resistant, detailed. | Art, medical scaffolds, construction. |
High-Quality Filaments for Superior Results
We partner with “COEX 3D” to offer premium, U.S.-made filaments. Choose from a variety of materials, including PLA, ABS, ASA, and specialty blends, to fit the exact requirements of your project.
🎁 Special Offer: Get 15% off COEX 3D filaments with code “3DPRINTINGBYKEVIN“. Plus, enjoy free shipping on orders over $49!
[Shop Filaments Now]
3. Applications of 3D Printing

3D printing has transformed industries by enabling faster prototyping, reducing waste, and allowing for customized designs. Here are examples of how it is used across sectors.
3.1. Medical Innovations
- Heart Valve Scaffolds (SL): Creates detailed heart valve models for surgical training and treatment research.
- Bone Scaffolds (BJ): Produces implants that mimic bone structure, encouraging tissue growth.
3.2. Aerospace and Automotive
- Lightweight Components (PBF): Produces durable yet lightweight robotic and aerospace parts.
- Repairing Dies (DED): Repairs expensive dies in automotive manufacturing, extending their lifespan.
3.3. Consumer Goods and Prototypes
- Custom Fashion (FDM): Designers use 3D printing for shoes, jewelry, and wearables.
- Edible Creations (BJ): Chefs and confectioners create intricate, edible sculptures using sugar or chocolate powders.
3.4. Pharmaceutical Applications
- Drug Delivery (FDM): Researchers print pills with layered medicine for customized release times.
- Bone Regeneration (SLS): Creates biodegradable scaffolds for growing new tissues.
4. 3D Printing and Industry 4.0
In the era of Industry 4.0, 3D printing stands as a cornerstone of innovation, offering flexibility and integration with intelligent systems.
- Mass Customization: Print personalized items—custom-fit implants, car parts, or fashion—without altering production lines.
- Sustainability: Reduces waste by using only the material required and enables localized production to cut carbon emissions.
- Smart Factories: Connect 3D printers to IoT systems for real-time monitoring and predictive maintenance.
5. Future Recommendations
To expand the potential of 3D printing, the following areas need development:
- Expanding Material Options: Invest in stronger, more sustainable materials like biocompatible metals or recyclable polymers.
- Enhancing Speed and Efficiency: Innovations like multi-nozzle systems could make large-scale production more feasible.
- Lowering Costs: Reducing printer and material costs will democratize access to this transformative technology.
- Promoting Education: Increase training in schools and workplaces to prepare a skilled workforce for additive manufacturing.
- Addressing Sustainability: Focus on biodegradable materials and closed-loop recycling systems.
Conclusion,
3D printing has evolved from a niche prototyping tool to a transformative technology, shaping industries from healthcare to aerospace. Its ability to create intricate shapes, reduce material waste, and enable on-demand production aligns perfectly with the goals of Industry 4.0. While challenges like cost and scalability remain, ongoing research promises to unlock even greater potential. As we refine materials, improve efficiency, and embrace sustainability, 3D printing will continue to revolutionize manufacturing and improve lives in unprecedented ways.
Glossary of Common 3D Printing Terms
To help beginners, here’s a quick reference for frequently used terms:
Additive Manufacturing: The process of building an object layer by layer, another name for 3D printing.
Filament: The thermoplastic material used in FDM printers resembles a spool of string.
Photopolymer: A liquid resin that hardens when exposed to UV light, used in stereolithography.
Sintering: The process of fusing powder particles together using heat or a laser without melting them completely.
Resolution: The level of detail a 3D printer can achieve, measured in microns (µm).
G-code: The programming language that tells a 3D printer how to move and build the object.
Tips for Beginners
Here are some quick tips to help those new to 3D printing: Start Simple: Use PLA filament with an FDM printer, as it’s easy to handle and forgiving for beginners.
Free Resources: Explore free 3D modeling software like Tinkercad or Blender to design your first prints.
Test Prints: Begin with small, simple designs like a keychain or a cube to learn how your printer behaves.
Maintenance: Keep your printer’s nozzle and bed clean to ensure successful prints.
Community Help: Join online forums or local maker spaces to learn from experienced users.
FAQs
Q: What’s the best 3D printer for beginners? A: FDM printers like the Creality Ender 3 or Prusa Mini are budget-friendly, reliable, and easy to use.
Q: How do I choose the right material? A: Start with PLA for ease of use. Move to ABS or PETG for more strength and flexibility, and use specialty materials (e.g., metal or TPU) as you gain experience.
Q: How much does 3D printing cost? A: A basic FDM printer costs $200–$500, with filament ranging from $20–$50 per spool. Advanced printers and materials can be significantly more expensive.