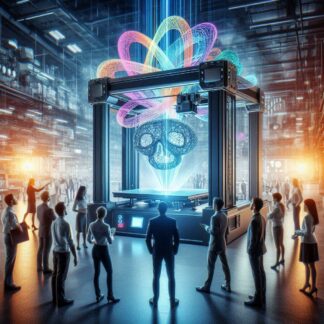
It’s becoming clear that 2025 isn’t just another year for makers—it’s the turning point where desktop 3D printing crosses from hobbyist niche into a frontier of streamlined creativity and smarter workflows. What was once a patchwork of manual tweaks and tinkering is quickly becoming a playground for automated precision and multi-material artistry. For those of us who’ve lived through the filament frustrations and first-layer anxieties, the progress feels personal. And powerful.
Today’s machines are not just printing—they’re problem-solving, predicting, and adapting. From one-click resin setups to printers that intuitively adjust to environmental shifts, the technology is finally meeting creators where we are: ready to build more, faster, with less compromise.
🔧 Tech That Thinks, Prints That Pop
Multicolor and multi-material printing used to be reserved for industrial rigs or endless spools and manual labor. Now, thanks to game-changers like the Bambu Lab A1 Mini and Creality’s K2 Plus, vibrant, layered models are no longer a hassle. These printers don’t just switch filaments—they orchestrate them. Whether you’re designing prototyped enclosures or complex figurines, color integration and hybrid components are becoming a seamless part of the workflow.
Beyond aesthetics, intelligence is the new standard. AI-assisted bed leveling, failure detection before errors even occur, and adaptive slicing tools are creating a safety net of precision that used to be unthinkable for desktop users. It’s democratizing detail in a way that’s making print-perfect creations more common than experimental flukes.
And let’s not forget the resin revolution. Printers like the ELEGOO Mars 5 and the Photon Mono M7 Max are redefining detail work. With 4K monochrome LCDs, auto-resin feeds, and self-calibrating sensors, these machines feel less like tools and more like collaborators—especially for those venturing into jewelry, character modeling, or dental prototyping.
⚡ Workflow That Doesn’t Waste Your Time
One of the most remarkable shifts this year is how much more control creators have over their time. Remote print monitoring has gone mainstream, with app integration that allows users to pause, stop, or troubleshoot prints while sipping coffee across town. The once-frantic dash back to the printer mid-job? Practically obsolete.
Speed has followed suit. Core XY designs, like those seen in the K2 Plus and Sovol SV07, are pushing boundaries by shortening print durations without sacrificing detail. For creators juggling multiple commissions or prototypes, this kind of throughput is a dream realized.
There’s also an embrace of batch production, particularly in resin setups. Auto-feed systems and larger build volumes mean your output scales with your ambition, not your patience. It’s not just about quicker prints—it’s about sustainable efficiency.
🧠 Creative Energy from the Community
Perhaps the most exciting part of this evolution is what creators are doing with it. The conversation has moved beyond “can I print this?” to “how do I print this better, smarter, and more functionally?” Modular designs are everywhere. Interlocking components for robotics, customizable camera mounts, functional furniture add-ons—you name it, someone’s prototyped it. The ingenuity is contagious.
Materials have followed suit. ASA filament is earning respect for its UV resistance and structural durability, while carbon fiber blends are introducing rigidity that holds up under pressure. Flexible filaments continue to expand what’s possible for wearable tech and experimental builds. If your toolbox includes ASA, chances are you’ve run into the same calibration dance I did. But when it locks in? The payoff’s unbeatable.
And let’s talk upgrades. Desktop printers are being modded into precision beasts. Enclosure kits, custom G-code, fan replacements, and firmware tweaks are part of a new maker vocabulary. Users are taking control of their rigs, not just using them but improving them—with confidence and creativity.
💬 My Take: Creativity Has No Gatekeeper
This isn’t just a tech wave—it’s a shift in ownership of innovation. What used to require industrial resources can now be done at a desk. Automation and smarter interfaces are dismantling the gatekeeping that kept so many creators on the sidelines. Whether you’re into artistic experimentation or functional prototyping, this movement proves that skill and imagination are the new currency—not expensive setups or institutional access.
Personally, I find this transition electrifying. I see it in my own journey—tweaking ASA filament settings on the CR-M4 or using AI tools to refine workflows. Each upgrade, each success or hiccup, contributes to a broader story: one where creators are in control, not just of tools but of outcomes.
🚀 Where Do We Go Next?
If you’re considering your first major upgrade, scouting new filaments, or planning a series of functional prints—2025 is the year to leap. I’d love to hear about your setup, your successes, and even your troubleshooting battles. Let’s build something great together.
And if you’re looking for curated links to the newest printers, slicers, or filament blends—I’ve got affiliate picks that align with everything covered above. Subscribers also get access to trend updates, insider hacks, and exclusive 3D printing tips you won’t find anywhere else.