Experience the transformation of manufacturing through 3D printing with end-use production. Uncover its significant benefits, overcome challenges, and explore the groundbreaking innovations shaping this technology’s future.
Picture a world where you can design a product and hold it in your hands within days or where you can create one-of-a-kind, sustainable items without the waste of traditional manufacturing. This isn’t just the stuff of sci-fi dreams anymore—it’s the reality of 3D printing for end-use production.
For decades, 3D printing was primarily a tool for rapid prototyping. But now, it’s evolved into a game-changing technology for manufacturing real, usable products. Industries like aerospace, automotive, healthcare, and even fashion are adopting this technology to redefine production.
If you’ve ever thought of 3D printing as a niche tool or an expensive novelty, it’s time to reconsider. You may be missing out on the next industrial revolution.
How 3D Printing Works
For those new to 3D printing, here’s a quick look at how it works:
- Digital Design: The entire process begins with creating a 3D model, which can be meticulously crafted using CAD (Computer-Aided Design) software. This software offers a range of tools that allow designers and engineers to create highly detailed and accurate representations of objects. Alternatively, one can also source a 3D model from a digital library, where numerous pre-made designs are available for various applications. These libraries serve as valuable resources, providing diverse models that can be readily accessed, modified, or integrated into more extensive projects, significantly streamlining the design process.
- Layer-by-Layer Printing: The 3D printer constructs the object by meticulously adding material one layer at a time. This process is precisely controlled by the digital design file, which dictates the object’s shape, dimensions, and details. Each layer is printed in succession, gradually forming the final piece as the printer moves in accordance with the specified blueprint. This layer-by-layer approach allows for intricate designs and complex geometries that are often impossible to achieve with traditional manufacturing methods.
- Materials: The types of materials used in printing can vary widely depending on the specific printer technology being employed. Common materials include various types of plastics, such as ABS and PLA, which are ideal for prototyping and everyday objects. Additionally, metals like aluminum, stainless steel, and titanium can be utilized for more durable and high-performance applications. Ceramics are also an option, offering aesthetic and functional benefits, especially in art and specialized industrial uses. Furthermore, advancements in 3D printing have introduced bio-compatible substances, which are particularly significant in the medical field for applications such as prosthetics and tissue engineering, allowing for the development of materials that are safe for human interaction and integration.
In contrast to traditional manufacturing techniques, which typically involve subtractive methods such as carving or molding materials to shape components, 3D printing operates through an additive process. This innovative technology constructs objects layer by layer, starting from a digital model.
Doing so significantly minimizes material waste, as only the necessary material is used to produce the final product. This enhances efficiency and contributes to sustainability in manufacturing, as less waste translates to a reduced environmental impact.
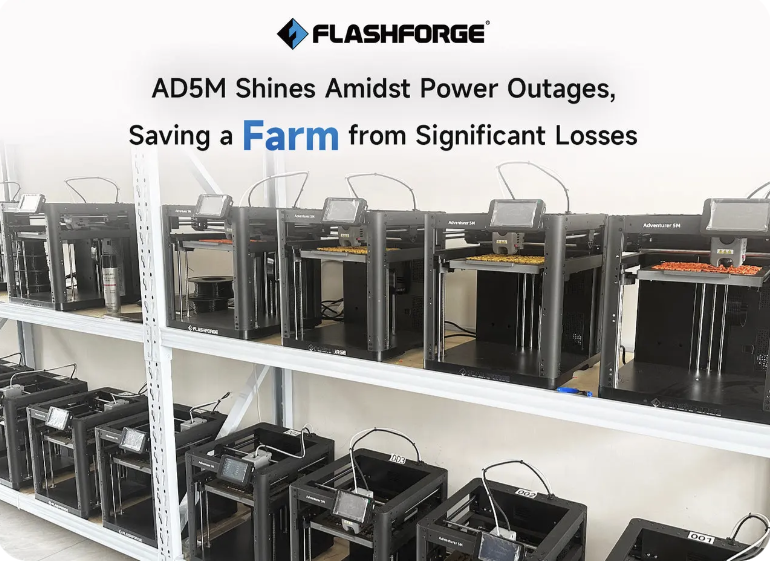
Why It’s Different from Traditional Manufacturing
Aspect3D PrintingTraditional Manufacturing
Setup Costs Low (no tooling needed) High (tooling, molds required)
Customization Easy and affordable Expensive and time-consuming
Waste Minimal (additive process) High (subtractive processes)
Speed for Prototypes The ability to transition from a concept to a finished product in a matter of days or even hours, as opposed to the weeks or months typically required by traditional manufacturing methods, makes 3D printing an appealing choice for end-use production.
This innovative process allows for rapid prototyping and immediate adjustments, which speeds up production timelines and enhances overall efficiency and creativity in design. As a result, 3D printing is gaining significant traction in various industries that are looking to streamline manufacturing processes.
Understanding End-Use Production
When we talk about end-use production, we’re referring to the manufacturing of finished, usable products—not just prototypes or concept models.
Industries across the board are embracing 3D printing to create functional, final-use components. Here are some examples:
- Aerospace: Lightweight brackets, turbines, and structural components.
- Healthcare: Patient-specific implants, prosthetics, and dental devices.
- Automotive: Custom car interiors, engine components, and specialty parts.
- Consumer Goods: Custom-fit shoes, jewelry, and even furniture pieces.
These are not just experimental applications; they represent real-world instances of how 3D printing is transforming the manufacturing industry.
Benefits of 3D Printing for End-Use Production
The question isn’t just why industries are embracing 3D printing; it’s why they’re embracing it now. Here are the key benefits:
Unparalleled Customization
Whether it’s a prosthetic limb tailored to an individual or a limited-edition shoe designed for a niche audience, 3D printing makes it easy to create one-of-a-kind products. Mass customization is no longer a luxury—it’s a reality.
Cost-Efficiency
Forget the need for expensive molds or tooling. With 3D printing, you can produce products on demand, reducing waste and cutting costs for small production runs.
Speed to Market
Time is money, and 3D printing lets manufacturers accelerate their timelines. You can iterate designs quickly and produce finished parts in a fraction of the time required by traditional manufacturing.
Design Freedom
Complex geometries that are impossible to make with traditional methods—think internal channels or intricate lattice structures—are easy with 3D printing.
Eco-Friendly Production
Sustainability is no longer optional. 3D printing uses only the material needed, significantly reducing waste. Plus, energy-efficient printers help lower the carbon footprint of manufacturing.
Case Studies: Real-World Success Stories
Still wondering how 3D printing is being applied in the real world? Here are some standout examples:
Aerospace: Flying High with Lighter Parts
A leading aerospace company used 3D printing to create titanium brackets for airplanes. These brackets were 30% lighter than traditionally manufactured parts, saving airlines millions in fuel costs while reducing emissions.
Automotive: Driving Customization Forward
An automotive manufacturer is using 3D printing to produce custom dashboard components and gear knobs for high-end vehicles. This allows customers to personalize their cars in ways that were previously impossible.
Healthcare: Saving Lives with Precision
A medical device company developed 3D-printed implants that match each patient’s anatomy perfectly. This not only improves surgical outcomes but also reduces recovery times.
These success stories show how 3D printing is making its mark across diverse industries.
Challenges and Limitations
While the advantages are clear, 3D printing has its challenges. Here are some of the challenges manufacturers face:
- Material Limitations: Many 3D printers are still limited to specific materials, though this is improving.
- Quality Control: Ensuring consistent quality across large production runs can be tricky.
- Certification: For regulated industries like aerospace or medical devices, meeting certification standards can be complex.
- Initial Investment Costs: Industrial 3D printers can be expensive, making it difficult for smaller businesses to adopt them.
That said, advancements in technology and materials are rapidly overcoming these barriers.
Future Prospects and Innovations
The future of 3D printing is bright, and the innovations on the horizon are nothing short of mind-blowing.
Emerging Trends:
- 4D Printing: Materials that can change shape or adapt to environmental conditions (like self-healing materials).
- AI Integration: Artificial intelligence optimizes print designs and automates quality control.
- Bio-Printing: Printing human tissues or organs for medical use is closer than you think.
- Construction Applications: Entire houses are being 3D printed in days, cutting labor and material costs.
Predictions for Adoption:
Experts forecast that by 2030, 3D printing technology is expected to evolve into a fundamental pillar of global manufacturing processes. This advancement will empower even small and medium-sized enterprises (SMEs) to manufacture products locally, reducing reliance on long supply chains and minimizing environmental impact.
As a result, businesses can produce items on demand, increasing efficiency and reducing waste. The accessibility of 3D printing will likely spur innovation, allowing for greater customization of products and fostering a more sustainable approach to manufacturing that prioritizes local resources and reduces carbon footprints.
Getting Started with 3D Printing
Want to explore 3D printing but not sure where to begin? Here’s a simple roadmap to get you started:
- Define Your Goals: Are you prototyping, customizing, or producing at scale?
- Choose the Right Printer: FDM printers are great for beginners, while SLA and SLS are suited for high-detail or industrial use.
- Select Materials: Research materials like PLA for prototypes, resin for detail, or metals for industrial parts.
- Learn CAD Basics: Tools like Tinkercad or Fusion 360 make designing 3D models easy.
- Start Small: Test with simple projects before scaling up to larger production runs.
Key Takeaways
- 3D printing is transforming manufacturing by enabling end-use production across diverse industries.
- The key benefits include customization, cost-efficiency, speed, and sustainability.
- While there are challenges, innovation is rapidly addressing them, making 3D printing more accessible.
- The future holds exciting developments, from 4D printing to bio-printing, that will further disrupt traditional manufacturing.
Final Thoughts: Don’t Get Left Behind
3D printing is not just a fleeting trend; it’s paving the way for the future of manufacturing! If you’re a small business owner, entrepreneur, or simply someone passionate about innovation, now is the perfect time to dive into this groundbreaking technology’s extraordinary possibilities. Unleash your creativity and discover how 3D printing can transform your ideas into reality!
Ready to take the first step? Research affordable 3D printers, start experimenting, or reach out to industry experts for guidance. The future of production is here—don’t miss your chance to be part of it.
Start Your 3D Printing Journey with KingRoon 3D Printers.
Ready to take the first step into the exciting world of 3D printing? Whether you’re a beginner experimenting with your first designs or a professional looking for high-performance equipment, KingRoon 3D Printers have you covered. Known for their affordability, precision, and reliability, KingRoon printers are the perfect choice for anyone looking to bring their ideas to life.
Right now, you can grab KingRoon 3D Printers on sale and start confidently creating! Don’t wait—this is your chance to join the 3D printing revolution without breaking the bank.
👉 Click here to shop KingRoon 3D Printers today!
The future of production is here, and it starts with your first print. Don’t miss out—take advantage of this deal and discover what 3D printing can do for you!
—
Happy Printing!
Bullwinkle