3D printing, or additive manufacturing, kicked off its journey with a pretty simple role—creating prototypes. It was a revolutionary technology for designers and engineers because it let them validate concepts quickly without waiting for traditional manufacturing and sticking just to prototyping. Nah, 3D printing had much bigger plans.
Over time, we’ve seen 3D printing move way beyond just models and mock-ups. It’s now a legitimate player in end-use production, meaning we’re making actual, functional products—stuff you can use right off the printer. This shift didn’t happen overnight; it’s been a gradual process with lots of trial and error, tech advances, and paradigm shifts in how we think about manufacturing.
Why does this shift matter? Simple. Traditional manufacturing involves tooling, molds, and a bunch of prep work. It’s time-consuming and often limited by design constraints. 3D printing, on the other hand, streamlines this process. We can produce complex geometries that are impossible with conventional methods and do it faster. This means quicker time-to-market, customized products and, surprisingly, cost savings in many cases.
The impact of this evolution is huge. We’re talking about redefining manufacturing processes, creating new business opportunities, and even having a positive environmental impact due to reduced waste and energy consumption. So, when you hear that 3D printing is just for prototypes, remember that it’s come a long way and is paving the way for the future of end-use production.
Technological Advancements Driving the Shift
The move from prototyping to end-use production wouldn’t be possible without some serious tech upgrades. One of the big game-changers? The materials themselves. We’ve gone from basic plastics to an array of advanced materials like high-performance polymers, metals, and even ceramics. This versatility opens up a ton of applications in various industries, each requiring different material properties.
Improved printer technology also plays a massive role. Today’s industrial 3D printers offer enhanced precision, speed, and reliability compared to their predecessors. With multi-material printing, we’re not limited to just one type of material per print. This capability allows for more complex and functional products, catering to industries that need mixed-material assemblies.
Another cornerstone driving this shift is the advancements in software and digital design tools. CAD software and simulation tools are way more sophisticated now, allowing for better design and optimization. These tools make it easier to create intricate, highly detailed models that can be directly fed into printers.
An often overlooked yet crucial aspect is post-processing enhancements. Improved finishing techniques have made it possible to produce parts that meet stringent quality and aesthetic standards. Smoothing, painting, and even metal plating can add the finishing touches that make 3D-printed objects indistinguishable from traditionally manufactured ones.
Integrating AI and machine learning has also been a game-changer. These technologies help optimize the printing process in real time, predicting failures and improving overall efficiency. AI-driven insights ensure that each print meets high-quality standards, which is vital for end-use applications.
The bottom line? These technological advancements collectively contribute to making 3D printing a viable option for end-use production across various industries. Staying on top of these evolving technologies is crucial. Whether you’re in manufacturing, healthcare, or any other industry leveraging 3D printing, keeping updated with these advancements can provide a competitive edge. 10kg 3D printing filament PLA/PETG starts from $89. CODE: “filament”
Industries Embracing 3D Printing for End-Use
Aerospace and defense sectors have been quick to see the benefits of 3D printing in end-use production. Lightweight, strong materials are essential for aircraft parts, and 3D printing excels in this area. Complex geometries can be produced that are not just lightweight but also incredibly strong, making them ideal for both commercial and military applications. Companies like Boeing and Lockheed Martin are already using 3D-printed parts in their aircraft and spacecraft, acknowledging the reliability and efficiency of additive manufacturing.
In healthcare, the applications of 3D printing are nothing short of groundbreaking. Custom prosthetics and implants tailored to individual patients are now a reality, offering a level of precision and personalization that’s impossible with traditional methods. Additionally, bioprinting—using bio-inks to create tissues and organs in the lab—brings us closer to solving organ shortage crises. Major hospitals and research institutions are investing heavily in these technologies, making healthcare more adaptable and patient-specific.
The automotive industry is another major player tapping into the potential of 3D printing. From producing high-performance parts quickly to enabling customized vehicle components, the scope is vast. Porsche, for instance, uses 3D printing to produce rare and vintage car parts that are no longer in production. This not only saves time but also makes it economically feasible to maintain and restore classic cars.
Consumer products have also seen a big impact. Brands are using 3D printing to offer customized products on demand, such as bespoke shoes, eyewear, and even furniture. This flexibility in design and production caters to the growing trend of personalization in consumer markets. Companies like Adidas have adopted 3D printing for their Futurecraft sneaker line, which benefits from the technology’s ability to create intricate designs that cater to individual comfort and style.
Industries across the board are finding innovative ways to integrate 3D printing into their production lines. Staying informed about these developments can provide valuable insights and inspiration for your own business strategies.
Case Studies of Successful End-Use Applications
One standout example comes from the aerospace industry, where GE Aviation has successfully integrated 3D printing into its production process. GE’s fuel nozzles for the LEAP engine are not only lighter but also five times more durable than traditionally manufactured parts. The move to additive manufacturing reduced the number of parts in the nozzle from 20 to just one, highlighting the efficiency and reliability of 3D printing in complex assemblies.
In healthcare, the story of patient-specific implants is compelling. Stryker, a leading medical technology company, uses 3D printing to create custom titanium implants for patients. This approach has resulted in quicker recovery times and better overall patient outcomes. Customization ensures the implants fit perfectly, reducing the risks associated with off-the-shelf solutions.
The automotive industry has its share of success stories, too. Bugatti leveraged 3D printing to manufacture a brake caliper for their high-performance sports cars. Using titanium and 3D printing technology, the caliper is lighter yet stronger than its conventional counterpart. This innovation not only improves vehicle performance but also paves the way for future advancements in automotive design and manufacturing.
In fashion and consumer goods, the collaboration between Adidas and Carbon stands out. Their partnership produced the Futurecraft 4D midsole, which uses 3D printing technology for a perfect blend of comfort and performance. The success of this product demonstrates how 3D printing can revolutionize the consumer goods industry by offering highly customizable and functional items that meet specific consumer needs.
One must also mention the impact 3D printing has had in the realm of architecture. Companies like Winsun in China are constructing entire homes using large-scale 3D printers. This method drastically cuts down construction time and costs while also reducing material waste. It’s an excellent example of how 3D printing is extending its reach into large-scale and high-impact projects.
These case studies provide a glimpse into the vast potential of 3D printing in end-use applications. By integrating this technology, businesses not only streamline their operations but also unlock new levels of innovation and efficiency. Whether you’re in an industry already leveraging 3D printing or just starting out, these examples can serve as both inspiration and practical guidance.
Cost-Benefit Analysis of 3D Printing for End-Use
Comparing the costs of 3D printing with traditional manufacturing can be an eye-opener. While the initial investment might seem steep because of advanced printers and high-quality materials, the long-term savings often justify the expenditure. Conventional manufacturing methods involve setup costs, tooling, and large-scale production runs to be cost-effective. On the other hand, 3D printing allows for small production batches and even individual units at a reasonable cost.
Production speed is another critical factor. Traditional methods may require weeks or even months for tooling and setup before mass production. In contrast, 3D printing can significantly shorten this timeline. Parts or products can go from digital design to finished items within days if not hours. This speed-to-market advantage is particularly valuable for industries where time is a crucial factor, like healthcare and consumer electronics.
Material waste is an often overlooked but vital consideration in the cost-benefit analysis. Traditional manufacturing techniques, especially subtractive methods like machining, generate significant material waste. 3D printing adds material layer by layer, resulting in less waste and a more sustainable process overall. This reduction in material usage not only lowers costs but also contributes to environmental sustainability initiatives.
Scalability can be a concern for businesses considering 3D printing for end-use production. Traditional methods are designed for mass production and can be more cost-effective at scale. However, advancements in 3D printing are starting to bridge this gap. Hybrid manufacturing systems that incorporate both traditional and additive techniques are emerging as cost-effective solutions for larger production volumes.
When evaluating the cost-effectiveness of 3D printing, it’s essential to look beyond the initial expenses. Factors in the long-term benefits include reduced waste, shorter production times, and the ability to create complex designs that would be impossible or prohibitively expensive using traditional methods. This comprehensive approach ensures that businesses can make an informed decision about integrating 3D printing into their end-use production processes. Exclusive $25 Off 3D Printers CODE: “share25”
Quality and Reliability in 3D Printed Products
Quality assurance is a major concern when it comes to end-use products, and 3D printing has made significant strides in this area. Modern 3D printers offer high precision and consistency, ensuring that each item produced meets stringent quality standards. Layer-by-layer construction, although different from traditional methods, can result in parts with excellent structural integrity and reliability.
One key advancement is the development of new quality control technologies. Non-destructive testing (NDT) methods, such as ultrasound and X-ray scanning, are now used to inspect 3D-printed parts for internal defects. This technology ensures that the products are not only precise but also durable and safe for end-use applications.
Certifications and standards also play a crucial role in ensuring product quality. Many industries, including aerospace and healthcare, require strict adherence to standards like ISO/ASTM 52900 or specific regulatory guidelines. Compliance with these standards is essential for gaining the trust of both regulators and customers. Companies that achieve these certifications demonstrate their commitment to producing high-quality and reliable products.
User testimonials and feedback add another layer of trust and reliability. Businesses that utilize 3D printing for end-use production often rely on user reviews to fine-tune their processes. Positive feedback serves as a testament to the efficacy and reliability of 3D-printed products in real-world scenarios. Listening to customer feedback can also highlight areas for improvement, ensuring continuous enhancement of quality.
By incorporating advanced quality control measures and adhering to industry standards, 3D printing continues to establish itself as a reliable method for producing end-use products. Investing in these quality assurance practices not only safeguards your product’s reputation but also builds customer trust and loyalty.
Challenges and Limitations in End-Use 3D Printing
While 3D printing offers numerous advantages, it’s not without its challenges and limitations. As exciting as the technology is, understanding these hurdles is crucial for anyone looking to integrate additive manufacturing into their production line.
One of the most pressing issues is the current limitation in materials. Not all materials are suitable for 3D printing, and even the ones that are available may not meet the specific requirements for certain applications. For example, while we’ve seen significant advancements in metal 3D printing, there are still limitations in terms of material properties and finish, which may not always match the quality of traditionally manufactured parts.
The speed and scalability of 3D printing also present challenges. While great for small batches, scaling up production to meet high-volume demands can be tricky. Many 3D printers are designed for prototyping rather than mass production, and transitioning them can be a logistical and financial challenge. Investing in multiple machines or hybrid systems can mitigate this, but it comes with its own set of complications and costs.
Another challenge lies in the post-processing stage. Unlike traditional manufacturing, where parts often come off the line ready for use, 3D-printed items usually require additional finishing steps. These can include removing support structures, surface finishing, and sometimes even heat treatments to achieve the desired properties. This additional labor and time can offset some of the efficiencies gained in the printing process itself.
From an economic standpoint, the initial setup costs for 3D printing can be a significant barrier. High-end industrial printers, materials, and skilled labor for operation require a considerable investment. While the long-term savings can be substantial, the upfront costs are something that businesses need to consider carefully.
Regulatory and compliance issues add another layer of complexity. Different industries have different standards, and not all 3D-printed parts can meet these stringent requirements easily. Navigating the regulatory landscape can be a time-consuming and costly affair, especially for industries like healthcare and aerospace, where certifications are incredibly rigorous.
Understanding these challenges helps set realistic expectations and prepares businesses for a smoother integration of 3D printing into their operations. Investing in research, training, and high-quality post-processing solutions can alleviate some of these issues and pave the way for more effective use of this groundbreaking technology.
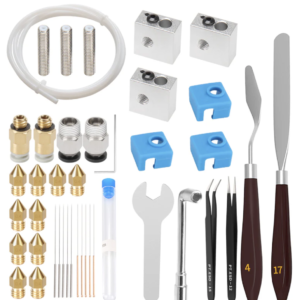
Future Trends and Innovations
The world of 3D printing is constantly evolving, and the future holds exciting possibilities. Emerging materials are one of the key areas to watch. We’re already seeing the development of new composites, biocompatible materials, and even food-grade substances, expanding the realms of what can be manufactured. Researchers are experimenting with materials that have properties like conductivity, flexibility, and even self-healing capabilities.
Another trend gaining traction is the integration of 3D printing with other advanced manufacturing processes. Hybrid manufacturing systems that combine additive and subtractive methods are becoming more common. This approach leverages the best of both worlds, allowing for greater design flexibility and higher-quality finishes. Combining 3D printing with technologies like CNC machining, robotic automation, and even AI-driven processes opens up new levels of innovation and efficiency.
The role of artificial intelligence and machine learning in 3D printing is another area poised for growth. AI can optimize designs for better performance, predict failures before they happen, and even customize products in real time based on data inputs. These AI-driven insights are set to make 3D printing smarter, faster, and more reliable.
Customization is becoming increasingly important, and additive manufacturing is perfectly suited to meet this demand. Mass customization allows companies to offer products tailored to individual needs and preferences without sacrificing production efficiency. From personalized medical implants to custom-fit athletic wear, the possibilities are endless.
Sustainability is another driving force behind future innovations. As environmental concerns become more pressing, 3D printing offers a way to reduce waste and energy consumption significantly. Companies are exploring ways to recycle materials and even use sustainable bio-based materials in their production processes. This focus on sustainability not only meets regulatory demands but also appeals to a growing segment of eco-conscious consumers.
Predictions for the future of 3D printing in end-use production are overwhelmingly positive. As technology and materials continue to advance, we can expect to see even more industries adopting additive manufacturing for a wider range of applications. Staying ahead of these trends and innovations will be crucial for businesses looking to leverage the full potential of 3D printing.
The Road Ahead for 3D Printing
3D printing has evolved far beyond its initial role in prototyping, stepping confidently into the realm of end-use production. This shift brings with it a host of advantages, from quicker time-to-market and reduced material waste to the ability to produce complex, customized items that meet specific industry needs.
The technological advancements driving this transformation are impressive. From new materials and improved printer technology to sophisticated software and AI, these innovations are making 3D printing more viable and advantageous for various sectors. Industries like aerospace, healthcare, automotive, and consumer products are already reaping the benefits and setting examples for others to follow.
While challenges and limitations do exist—such as material constraints, scalability issues, post-processing requirements, and regulatory hurdles—these are not insurmountable. Ongoing research, training, and investments in quality control can help mitigate these challenges, paving the way for broader adoption.
Looking to the future, the trends and innovations emerging in the 3D printing space are incredibly promising. Whether it’s the development of new materials, integration with other manufacturing processes, or advancements in AI and sustainability, the potential for growth is enormous. Businesses that stay ahead of these trends and invest in this technology early will likely enjoy a competitive edge.
The road ahead for 3D printing in end-use production is full of opportunities. By understanding the current landscape and preparing for future advancements, companies can position themselves to take full advantage of what 3D printing has to offer. As this technology continues to evolve, its impact on manufacturing and production processes will only grow, opening up new horizons for innovation and efficiency.
Get the Best Price On 3D Printing Tools ! Click Here!
Bullwinkle