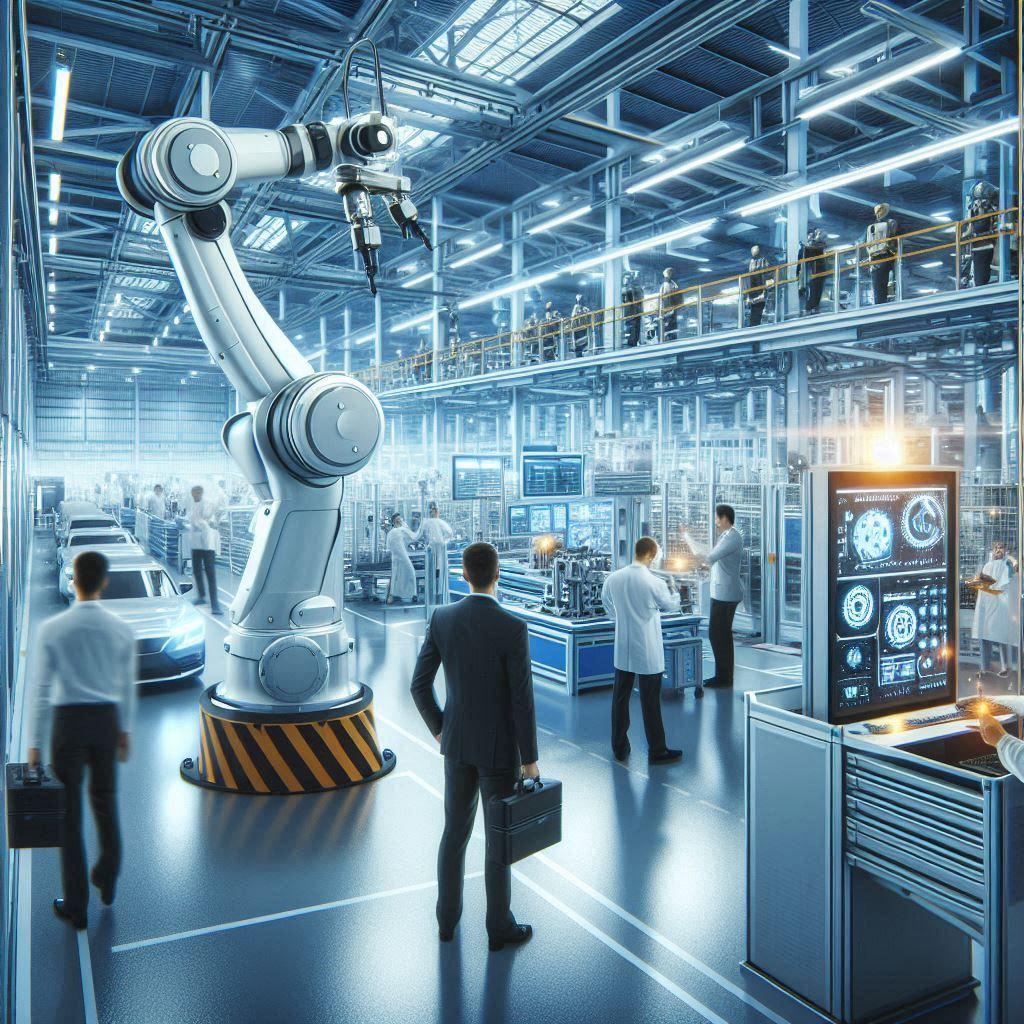
How Creality Printers Combine CNC Machining
As a professional copywriter, I’ve closely watched manufacturing technology evolve. One of the most compelling developments recently has been hybrid manufacturing, an approach that seamlessly blends traditional CNC machining with innovative 3D printing techniques. Today, companies like Creality are at the forefront, empowering businesses and hobbyists to achieve unprecedented levels of precision and efficiency.
Hybrid manufacturing isn’t just a passing trend; it’s reshaping production methods by marrying the strengths of traditional and digital processes. While CNC machining has long been valued for its precision and consistency, it often falls short when dealing with complex geometries or lightweight structures. Conversely, 3D printing excels in creating intricate, lightweight, and customized designs but typically lacks the ultra-precise finish and strength that CNC machining delivers.
Creality’s innovative approach bridges this gap effectively. Their advanced 3D printers are increasingly integrated into hybrid setups, allowing users to initially build complex geometries layer by layer, and then refine and perfect them through precise CNC machining. This combination significantly enhances the overall quality and durability of the final product.
From my experience, one of the most significant advantages of hybrid manufacturing with Creality printers is the dramatic increase in efficiency. For example, by printing intricate shapes or internal structures first, manufacturers drastically reduce material waste—something that traditional machining alone often struggles to achieve. Once the initial form is printed, CNC machines step in to precisely finish surfaces, drill exact holes, and add critical details, ensuring the final product meets stringent tolerances.
Additionally, the combined approach significantly reduces production time. Traditional manufacturing can require multiple steps, including casting, milling, and assembly, each involving lengthy processes. Hybrid setups streamline this workflow, allowing complex parts to be produced in fewer stages and with fewer resources. This not only cuts down lead times but also reduces overhead costs significantly.
In practical applications, industries ranging from automotive to aerospace and medical devices are rapidly adopting hybrid methods. Creality printers, known for their reliability and affordability, provide businesses of all sizes an entry point into sophisticated manufacturing methods that were once exclusive to larger corporations with extensive budgets.
For instance, in aerospace applications, hybrid manufacturing facilitates the creation of lightweight yet robust components, crucial for performance and safety. Meanwhile, in the medical field, it allows for precise, customized implants and prosthetics tailored specifically to patients’ anatomy—improving outcomes and comfort dramatically.
Moreover, Creality continues to refine their printers, integrating advanced features such as AI-driven optimization and real-time monitoring. These enhancements ensure that each print is executed flawlessly, with minimal downtime or errors, further boosting the effectiveness of hybrid manufacturing setups.
From my perspective, hybrid manufacturing represents the future of precise and efficient production. By harnessing the strengths of both CNC machining and 3D printing, companies utilizing Creality’s solutions are positioned to achieve superior results, drive innovation, and stay competitive in an ever-evolving marketplace.
Have you explored hybrid manufacturing yourself, or are you considering integrating these methods into your workflow? I’d love to hear your thoughts and experiences—feel free to share them below.
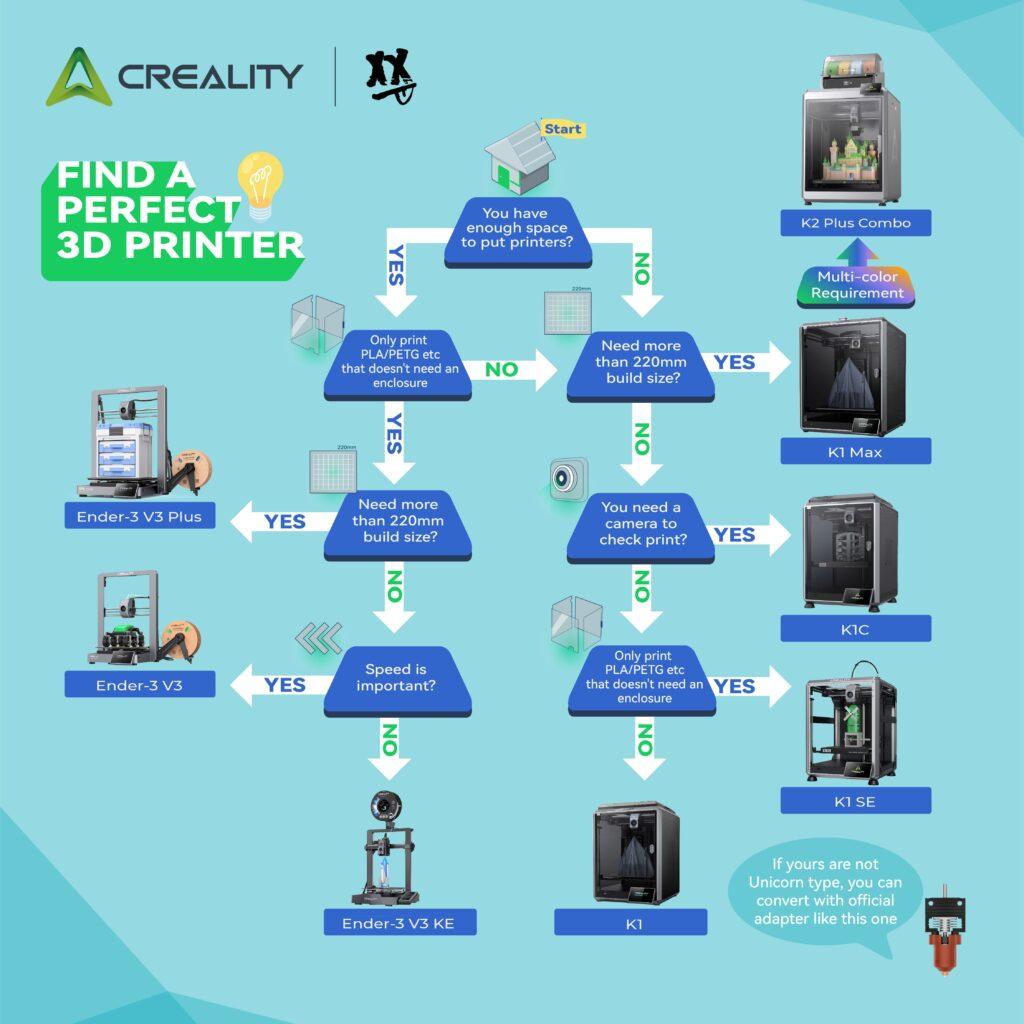