Curious about multi-material 3D printing? Discover how desktop 3D printers like the Prusa XL, Creality K2 Plus Combo, and Aerosint SPD are making it easier than ever to combine materials for functional, artistic, and even commercial creations. Dive into the future of DIY fabrication.
Imagine printing a robotic arm with flexible joints, rigid supports, and conductive pathways—all in one go. No wires to insert, no pieces to glue together. Just hit “Print” and watch it come to life layer by layer. Not long ago, this kind of fabrication sounded like something reserved for industrial labs or high-end engineering firms. But today? It’s becoming something hobbyists can do from their garage, educators can use in classrooms, and small businesses can leverage for product development.
Welcome to the exciting world of multi-material 3D printing on desktop machines—a game-changing leap in additive manufacturing.
What Is Multi-Material 3D Printing?
Let’s keep it simple. Traditional 3D printing uses one material—usually plastic—to build objects layer by layer. That’s great for basic models and simple parts, but what if you want your print to have multiple properties? Say, a soft rubber grip on a hard plastic handle? Or a model that combines metal-like strength with lightweight resin?
That’s where multi-material 3D printing comes in.
It allows one printer to combine different materials with distinct characteristics—like flexibility, hardness, color, or even electrical conductivity—into a single object. This opens up a whole new world for creativity, functionality, and real-world applications.
Why It Matters: Real Uses for Real People
Let’s not just talk tech. Let’s talk life.
For educators, multi-material printers mean you can print out a full model of the human heart—with soft, flexible valves and rigid arteries. Students can hold it, feel it, and understand anatomy in a way no textbook ever could.
For hobbyists, imagine crafting a cosplay mask with hard, detailed armor parts and flexible, wearable straps in one print. No glue. No mess. Just pop it off the bed and put it on.
And for small businesses or startups, this tech allows you to prototype fully functional products—think sunglasses with soft nose pads or wearable devices with built-in circuits—without outsourcing to expensive production lines.
That’s not the future. That’s now.
How It Works: The Tech Behind the Magic
1. Tool Changing Systems
This is what Prusa XL is known for. It uses multiple independent tool heads—up to five—that automatically swap in and out during the print. Each tool head can be loaded with a different filament, meaning you can use PLA in one, TPU in another, PETG in a third, and so on. The printer knows when to switch tools, making the process seamless.
Bonus: Because each tool head is independent, there’s less mess and waste compared to older multi-material methods that relied on pushing multiple filaments through one nozzle.
2. Filament Switching or Color Mixing
The Creality K2 Plus Combo takes another route. Rather than using separate tool heads, it uses a single nozzle that can handle up to 16 different filaments, switching between them automatically. It’s a bit like a color-mixing pen but for 3D filaments. While it might not offer the same level of precision as independent tool heads, it excels at vibrant, colorful prints and smart filament management—great for artistic or visually complex projects.
3. Powder-Based Multi-Material Deposition
Then there’s Aerosint’s SPD (Selective Powder Deposition)—which is more of a technology platform than a specific printer model. Instead of using spools of filament, it uses powders—like metal, ceramic, or polymer powders—and deposits them selectively in each layer. That means you can literally print a part that’s metal on the outside, ceramic in the middle, and plastic at the base. This is advanced stuff and points toward the future of hybrid manufacturing on a desktop scale.
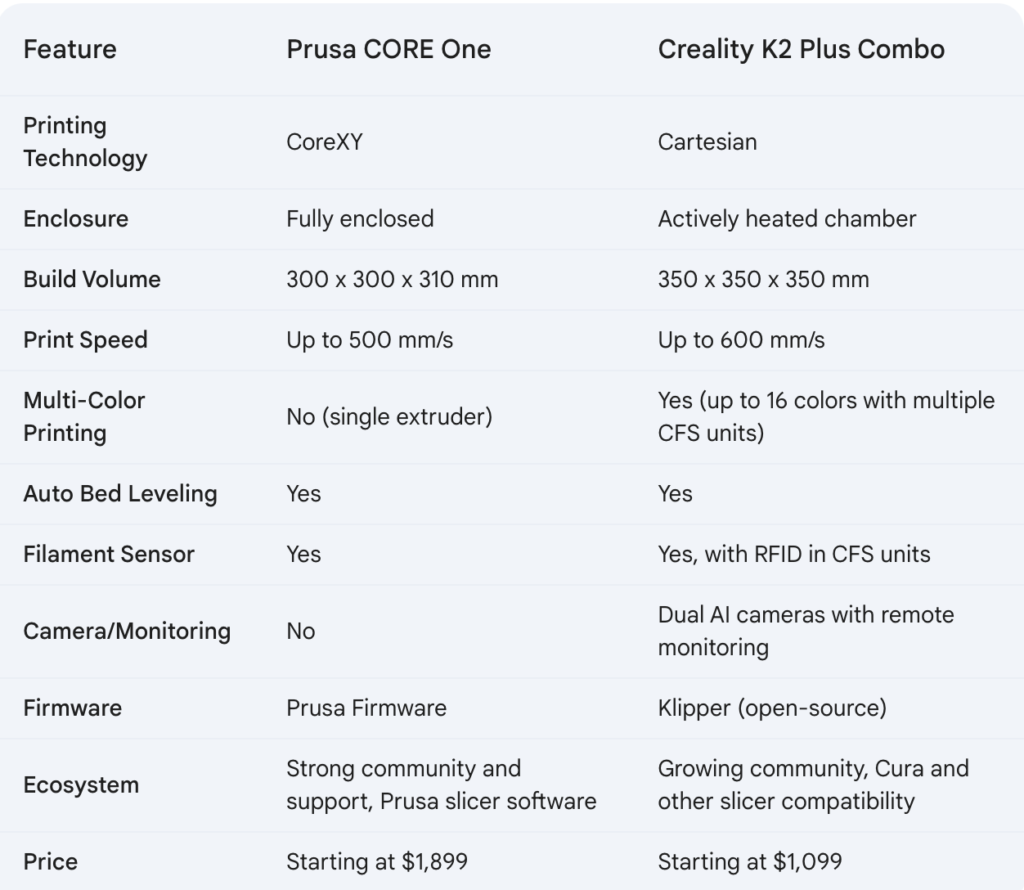
Meet the Machines: Desktop Printers Pushing the Limits
Let’s take a closer look at the players making this all possible.
🧰 Prusa XL: The Prototyper’s Dream
Why it’s impressive: The Prusa XL is built for precision and flexibility. With its modular tool-changing system, you can load up to five tool heads, each with a different filament. This means you can create prints with both flexible and rigid sections, different colors, or even support material that dissolves in water.
Who it’s for: Engineers, designers, serious makers.
What makes it special: Prusa’s open-source reputation and obsessive attention to detail. The XL has been battle-tested in beta and praised for its minimal waste, high uptime, and easy calibration.
Real-life use case: A product design firm prints a smartwatch case using TPU for the band and PETG for the rigid body—all in one job. No assembly, no outsourcing.
🎨 Creality K2 Plus Combo: The Artist’s Canvas
Why it’s impressive: This machine isn’t just fast—it’s versatile. With support for up to 16 colors or materials, the K2 Plus Combo is ideal for users who want to get creative without sacrificing print quality or ease of use.
Who it’s for: Artists, educators, small business owners.
What makes it special: It’s loaded with smart features like auto-bed leveling, filament run-out detection, and intelligent color management. Plus, the Creality ecosystem is beginner-friendly and well-supported.
Real-life use case: A small Etsy shop designs multi-colored planters with rigid bodies and soft, non-slip bases. They’re selling out faster than they can print them.
⚙️ Aerosint SPD Technology: A Glimpse Into the Future
Why it’s impressive: Aerosint’s powder-based approach is entirely different. By layering multiple types of powders, the technology can produce parts that are structurally, functionally, and aesthetically complex.
Who it’s for: Advanced users, research labs, industrial prototyping.
What makes it special: The ability to combine materials like metal and ceramic—not just different plastics—sets Aerosint apart. It’s still on the cutting edge but showing real promise for wider adoption.
Real-life use case: A university lab prints heat-resistant drone components with internal ceramic cores and metal exteriors—lightweight, strong, and ready for testing.
Challenges of Multi-Material Printing—and How They’re Being Solved
No revolution comes without growing pains.
🧩 Calibration and Setup
Multi-material setups require more fine-tuning than single-material printers. Different materials shrink at different rates or need different temperatures. But newer printers like the Prusa XL and Creality K2 Plus come with smart calibration systems that auto-adjust settings.
💸 Cost
Multi-material 3D printers can be pricey—especially those with tool changers or powder systems. But as demand rises and competition grows, prices are coming down. You can now get capable multi-material setups for under $1,000, depending on your needs.
🔄 Material Compatibility
Not all materials play nice together. Some bond poorly, or even degrade each other over time. But manufacturers are developing new multi-material-compatible filaments and creating databases of validated combinations to make experimentation safer and easier.
The Ripple Effects: Why This Trend Matters
Multi-material printing isn’t just a new feature—it’s a shift in mindset. Instead of thinking of 3D printing as just making plastic models, we’re now looking at it as true desktop manufacturing. This impacts everything from education to entrepreneurship.
🎓 In Classrooms
Kids can learn engineering concepts by printing functional gears, soft grips, or circuit housings. Science, art, and tech collide—hands-on.
🛠️ In Small Businesses
Entrepreneurs can prototype and even manufacture custom goods in-house, on-demand. No need for injection molds or outsourcing.
🎨 In Creative Spaces
Artists can bring wild concepts to life with new textures, forms, and material blends that were previously impossible or unaffordable.
Where It’s Going: The Next 5 Years
Here’s the exciting part: We’re just getting started.
In the next few years, expect to see:
- More accessible pricing as technology scales
- Materials with smarter properties, like shape memory or embedded sensors
- AI-assisted print planning for optimal material use and fewer failures
- Community-driven content, with open libraries of tested multi-material designs
As software gets smarter and hardware more precise, the barrier to entry continues to fall.
Final Thoughts: Printing Possibilities, Not Just Objects
Multi-material 3D printing is more than a technical achievement—it’s a creative unlock. It allows makers to think in terms of function, not just form. What used to require multiple machines, tools, and hours of post-processing can now be done on a single printer sitting on your desk.
Whether you’re a hobbyist printing your next cosplay upgrade, a teacher bringing STEM to life, or a small business chasing your next product idea, multi-material printing is making things possible that weren’t before.
And the best part? The tools are finally in your hands.
Ready to print your ideas in color, texture, and functionality? The desktop 3D printer market is wide open. All you have to do is hit “Start.”