Welcome to the Future of Supply Chains
Imagine a world where businesses can create products exactly when and where they need them. No more long waits for shipments to arrive from across the globe. No more delays because of factory closures or transportation issues. This is the incredible potential of 3D printing, or as it’s known in the industrial world, additive manufacturing (AM).
Supply chains—those unseen networks that bring products from factory floors to store shelves—are the backbone of every industry. Without them, we wouldn’t have the smartphones in our hands, the clothes on our backs, or even the food in our kitchens. Yet, despite their importance, traditional supply chains are often slow, costly, and vulnerable to disruptions. One little hiccup and the entire system can grind to a halt.
But things are changing and fast. Supply chains are undergoing a revolution thanks to the exciting technology of additive manufacturing. This technology isn’t just shaking things up—it’s transforming the way we think about manufacturing, production, and global supply chains. In this blog, we’re going to explore exactly how 3D printing is revolutionizing supply chains, making them faster, more flexible, and much more resilient to the unpredictable world around them.
Additive Manufacturing in Supply Chain: A New Age of Flexibility
On-Demand Production: Goodbye, Warehouses!
Let’s start with one of the most exciting aspects of 3D printing—on-demand production. In traditional manufacturing, companies have to produce goods in large quantities, store them in warehouses, and ship them out as orders come in. But with 3D printing, this is no longer necessary. Imagine being able to produce exactly what you need, exactly when you need it!
Instead of manufacturing thousands of parts ahead of time, companies can now produce parts on demand. This is a huge deal because it eliminates the need for expensive warehouse space, reduces waste, and cuts down on the cost of shipping products back and forth between different parts of the world.
Think about it like this: with traditional manufacturing, you’re basically baking hundreds of cookies, hoping that people will buy them all. But with 3D printing, it’s like you have a magical oven that can bake a cookie the moment someone orders one. No waste, no storage, just instant satisfaction.
This flexibility is a game-changer. This means businesses can respond quickly to changing customer demands without the delays caused by waiting for new shipments to arrive. Customization becomes easier, too—products can be tailored to individual customer preferences without the need for large-scale production changes. All of this creates a supply chain that’s more efficient, more responsive, and way more customer-friendly.
Reduction of Dependency on Traditional Manufacturing Processes
For years, companies have been tied to complex and often fragile manufacturing processes. Goods are typically produced in large factories, often located in countries halfway around the world. Once products are made, they’re shipped thousands of miles, passing through countless checkpoints and distribution centers before finally reaching their destination.
But here’s the thing—this system is vulnerable. If a factory shuts down, if shipping routes are disrupted, or if a part gets delayed, the entire supply chain can be thrown into chaos. And let’s face it, disruptions happen all the time—from natural disasters to global pandemics to political conflicts.
Enter additive manufacturing. With 3D printing, businesses can greatly reduce their dependency on traditional manufacturing processes. Instead of relying on distant factories and complex logistics, companies can set up localized production hubs closer to where their customers are. These hubs can produce parts using 3D printers, reducing the need for international shipping and minimizing the impact of global supply chain disruptions.
This shift to local production makes supply chains faster, more resilient, and more sustainable. And it’s not just about speed—companies can also experiment with new designs and materials more easily, leading to greater innovation. The days of waiting for parts to be shipped halfway around the world are coming to an end, and 3D printing is leading the charge.
Resilience in the Face of Disruptions: A Supply Chain That Can Bounce Back
Now, let’s talk about resilience. If there’s one thing we’ve learned in recent years, it’s that supply chains are vulnerable to disruptions. Whether it’s a factory closure, a natural disaster, or a global pandemic, supply chains can break down in an instant, leaving businesses scrambling to recover.
Yet, with 3D printing, companies can build resilience in their supply chains. How? By decentralizing production and making it easier to adapt to changing circumstances.
Here’s how it works: with traditional manufacturing, if one part of the supply chain goes down—say, a factory in another country—the whole process can be delayed. However, with 3D printing, companies can set up multiple production hubs in different locations. If one hub is disrupted, production can be shifted to another hub, minimizing downtime and keeping the supply chain moving.
This decentralized approach also makes it easier to respond to sudden spikes in demand. Imagine a medical company needing to produce a large number of ventilator parts during a health crisis. With traditional manufacturing, this might take weeks or even months. Nevertheless, with 3D printing, production can be ramped up quickly, ensuring that essential products are delivered where they’re needed most.
In short, additive manufacturing creates a supply chain that’s just faster and more flexible—it’s also stronger and more capable of withstanding disruptions. Whether it’s a sudden crisis or a gradual shift in customer demand, 3D printing enables companies to adapt and thrive, no matter what the world throws its way.
Impact on Industries: Who’s Embracing 3D Printing?
Now that we’ve covered the basics of how 3D printing is changing supply chains let’s take a closer look at some of the industries that are leading the charge. From aerospace to healthcare, additive manufacturing is transforming the way businesses operate, making them more efficient, innovative, and responsive.
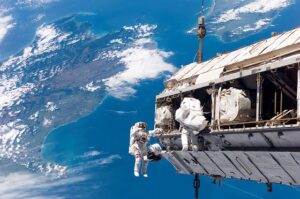
Aerospace: Lighter, Faster, Stronger
The aerospace industry has long been at the forefront of technological innovation, and 3D printing is no exception. In this field, every ounce counts. Lighter parts mean lighter aircraft, which translates to lower fuel consumption and reduced costs. But traditionally, creating lightweight parts has been a challenge—enter 3D printing.
With additive manufacturing, aerospace companies can produce parts that are not only lighter but also stronger and more durable than traditional components. This is because 3D printing allows for more complex designs that can be achieved with conventional manufacturing methods. For example, engineers can create hollow structures or intricate lattice designs that maintain strength while reducing weight.
But it’s not just about making lighter planes—3D printing also speeds up the production process. Instead of waiting weeks or months for parts to be manufactured and shipped, companies can print parts on-demand, drastically reducing lead times. This ability to produce parts quickly and locally is especially valuable for the aerospace industry, where precision and speed are critical.
Learn more here– CR-Scan Otter 3D Scanner
Automotive: Driving Innovation Forward
The automotive industry is another major player in the 3D printing revolution. Car manufacturers are increasingly using additive manufacturing to produce custom parts, prototypes, and even entire car components. This allows them to experiment with new designs and bring products to market faster than ever before.
In the past, creating a prototype for a new car model could take months of planning, designing, and testing. However, with 3D printing, this process can be significantly shortened. Designers can quickly produce prototypes, test them, and make adjustments on the fly. This rapid prototyping enables car manufacturers to innovate faster, bringing new models to market in record time.
But the benefits don’t stop there. 3D printing also allows for the creation of customized parts, which is becoming increasingly important as consumers demand more personalized products. Whether it’s a custom dashboard, unique interior design, or specialized engine components, 3D printing makes it possible to produce one-of-a-kind parts without the need for expensive retooling.
In the future, we may even see fully 3D-printed cars! While this might sound like science fiction, several companies are already experimenting with 3D-printed vehicle components, paving the way for a new era of automotive manufacturing.
Healthcare: Personalized Medicine and Beyond
Perhaps one of the most exciting applications of 3D printing is in the healthcare industry. From creating personalized prosthetics to printing human tissue, additive manufacturing is revolutionizing the way medical professionals approach patient care.
One of the biggest challenges in healthcare is that every patient is different. Traditional mass-produced medical devices often don’t fit perfectly, leading to discomfort or even complications. However, with 3D printing, doctors can create customized prosthetics, implants, and surgical tools that are tailored to each individual patient’s unique anatomy.
For example, instead of using a generic hip implant, surgeons can now use 3D printing to create an implant that fits perfectly with the patient’s bone structure. This not only improves comfort but also increases the chances of a successful surgery and faster recovery.
However, the applications of 3D printing in healthcare go beyond just prosthetics. Researchers are also exploring the potential for bioprinting, where human cells are used to create tissues and organs. While we are still in the early stages of this technology, the possibilities are endless. Imagine being able to 3D print a kidney for a transplant patient, eliminating the need for organ donors and reducing waiting times.
Consumer Goods: Customization at Your Fingertips
From sneakers to furniture, the consumer goods industry is also embracing 3D printing in a big way. In an age where consumers are increasingly seeking personalized products, additive manufacturing offers a way to meet that demand.
Take the fashion industry, for example. Brands are using 3D printing to create unique, custom-designed shoes and accessories. Instead of mass-producing a single design, they can offer customers the option to create something that’s truly one-of-a-kind. This not only enhances the customer experience but also reduces waste, as products are only created when they are ordered.
Similarly, in furniture design, 3D printing allows for greater creativity and flexibility. Designers can experiment with new shapes, materials, and designs that would be difficult or impossible to achieve with traditional manufacturing techniques. This leads to more innovative products and gives consumers greater freedom to customize their purchases.
Learn more here–CR-Scan Raptor 3D Scanner
The Future of Supply Chains Is Here
So, what have we learned? Additive manufacturing is no longer just a buzzword—it’s a powerful tool that’s revolutionizing the way industries approach supply chains. From on-demand production to improved resilience and flexibility, 3D printing is transforming the way products are made, shipped, and delivered.
Supply chains that once relied on complex, global networks are now becoming more localized, agile, and responsive. Industries from aerospace to healthcare to consumer goods are already reaping the benefits of 3D printing, and we are only scratching the surface of what this technology can do.
Looking ahead, the future of supply chains is bright. As 3D printing technology continues to advance, we can expect to see even more innovative solutions that make supply chains faster, smarter, and more resilient. Whether it is through the creation of new materials, the development of more efficient printers, or the integration of artificial intelligence, additive manufacturing is poised to play a central role in shaping the future of global production.
Ender-3 V3 KE 3D Printer
In a constantly changing world, one thing is clear:
“3 printing is here to stay,” and it is revolutionizing supply chains in ways we are beginning to understand. So, keep your eyes peeled—because the future is being printed, one layer at a time!
To Explore Further
3D printing is evolving rapidly, and several exciting trends are shaping the industry in 2024:
- Widespread Adoption Across Industries: 3D printing is increasingly integrated into various sectors, including aerospace, defense, medical devices, and consumer goods. This widespread adoption is driven by significant advancements in additive manufacturing (AM) technology1.
- Supply Chain Innovation: AM is crucial in mitigating supply chain disruptions. By enabling on-demand production and reducing dependency on traditional manufacturing processes, 3D printing is helping industries become more resilient1.
- Sustainability Efforts: There is a growing focus on sustainability within the 3D printing industry. Companies are exploring eco-friendly materials and processes to reduce waste and energy consumption1.
- Advancements in Materials: The development of new materials, including high-performance polymers and metals, is expanding the applications of 3D printing. These materials are enabling the production of more complex and durable parts.
- Integration with AI: Artificial intelligence is being integrated into 3D printing workflows to optimize designs, improve quality control, and enhance overall efficiency. AI-driven tools are helping to automate and streamline the additive manufacturing process1.
- Medical and Dental Applications: The medical and dental fields are seeing significant benefits from 3D printing, with advancements in custom prosthetics, implants, and even bioprinting of tissues and organs1.
- Consumer Goods and Customization: 3D printing enables greater customization in consumer products, from personalized fashion items to bespoke home decor. This trend is driven by the demand for unique and tailored products1.
These trends highlight the transformative potential of 3D printing across various industries.
Please leave your comments or questions below.
Bullwinkle