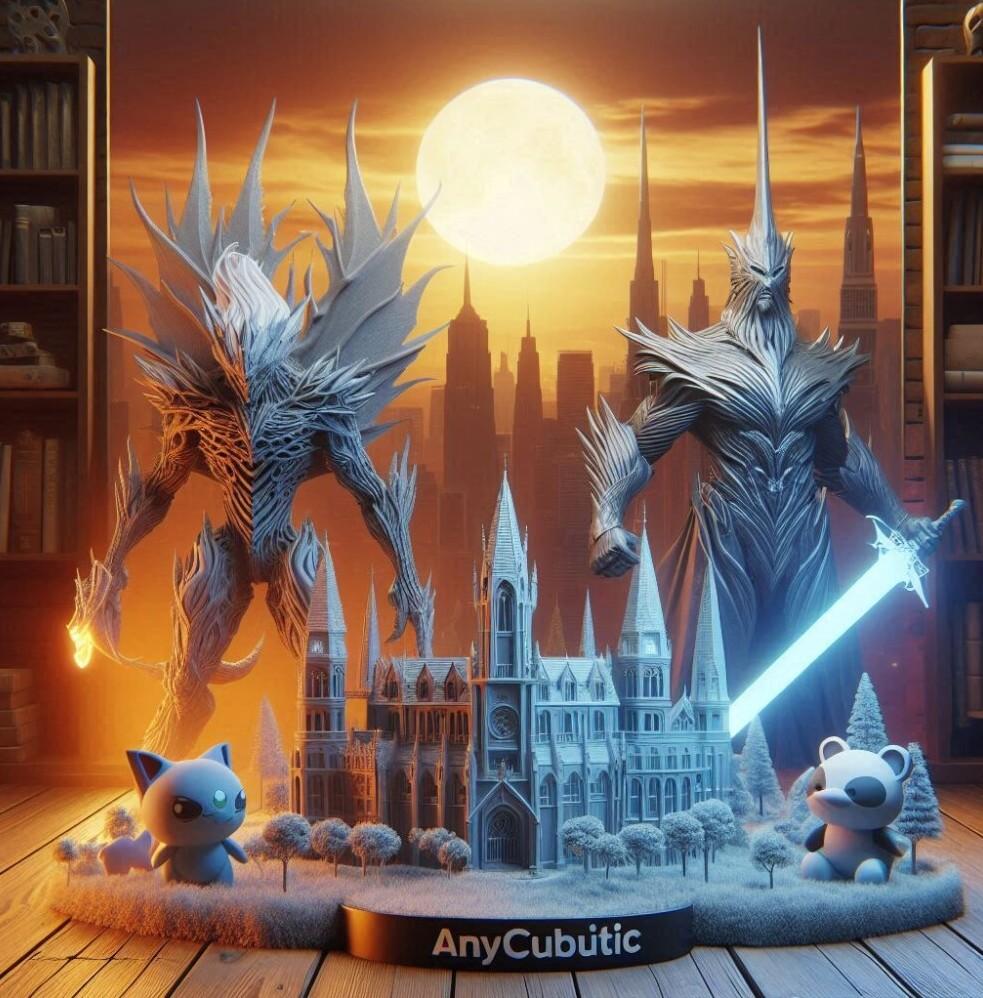
Unlock peak performance from your hobbyist 3D printer! This comprehensive guide covers essential troubleshooting tips, routine maintenance, and expert advice to ensure smooth operation, high-quality prints, and an extended printer lifespan. Perfect for beginners and experienced makers alike.
The Heart of Your Hobby
Your hobbyist 3D printer is more than just a machine; it’s a gateway to bringing your digital designs to life. From intricate miniatures for tabletop gaming to functional prototypes for a new invention, or even whimsical artistic creations that add a personal touch to your home, the possibilities are virtually limitless. This incredible technology puts the power of creation directly into your hands, transforming concepts into tangible objects with layers of melted plastic.
However, like any sophisticated tool, 3D printers require a bit of care and understanding to perform at their best. Just as a seasoned chef meticulously maintains their knives or a musician fine-tunes their instrument, a dedicated maker knows that consistent, high-quality prints stem from a well-maintained and properly functioning machine. Even the most advanced printers can encounter frustrating glitches—a print that suddenly detaches from the bed, layers that refuse to align, or a nozzle that stubbornly refuses to extrude. These hiccups can be discouraging, but they don’t have to be roadblocks.
This comprehensive guide is designed to empower you with the knowledge and practical skills needed to keep your 3D printer in top condition. We’ll delve into common troubleshooting scenarios, offering clear solutions to get you back on track quickly. More importantly, we’ll outline a proactive maintenance schedule, transforming potential problems into minor inconveniences. By embracing these essential practices, you’ll not only extend the lifespan of your valuable equipment but also consistently achieve the precise, beautiful prints you envision, making your 3D printing journey smoother and infinitely more rewarding.
Decoding Common 3D Printing Problems and Their Solutions
Even the most seasoned 3D printing enthusiasts encounter hiccups. Here’s a rundown of common issues, their likely causes, and practical solutions:
Problem 1: Poor First Layer Adhesion
This is perhaps the most frustrating issue, as a failed first layer often means a failed print.
- Symptoms: Prints detaching from the build plate, warped edges, uneven first layer.
- Likely Causes:
- Improper Bed Leveling: The nozzle is too far or too close to the print bed.
- Dirty Print Surface: Residue (fingerprints, dust, old filament) can reduce adhesion.
- Incorrect Bed Temperature: Too cold, and the material won’t stick; too hot, and it can warp.
- Incorrect Nozzle Temperature: Not hot enough for the filament to flow properly and adhere.
- Warped Print Bed: An uneven surface, often due to manufacturing defects or prolonged heat cycling.
- Solutions:
- Re-level Your Print Bed: This is paramount. Use the printer’s auto-leveling function (if available) or manually level using the paper method at multiple points.
- Clean the Print Surface Thoroughly: Use isopropyl alcohol (IPA) for most surfaces, or soap and water for PEI sheets.
- Adjust Bed Temperature: Refer to your filament manufacturer’s recommendations. Common settings are 50−60∘C for PLA and 80−100∘C for ABS/PETG.
- Optimize Nozzle Temperature: Ensure it’s within the filament’s recommended range.
- Use Adhesion Aids: Gluestick, hairspray (unscented, extra-hold), or specialized build plate adhesives can help.
- Consider a Different Build Surface: Glass, PEI, or flexible magnetic plates offer different adhesion properties.
- Check for Drafts: Keep your printer away from open windows or fans, as sudden temperature drops can cause warping.
Problem 2: Stringing and Blobs
These aesthetic imperfections can significantly detract from print quality.
- Symptoms: Fine strings of filament between printed parts, small blobs or zits on surfaces.
- Likely Causes:
- Incorrect Retraction Settings: Not enough retraction, or retraction speed is too slow/fast.
- Excessive Nozzle Temperature: Filament becomes too molten and oozes.
- Wet Filament: Moisture absorbed by the filament can cause bubbling and stringing.
- Solutions:
- Calibrate Retraction Settings: Adjust retraction distance and speed in your slicer. Start with small increments (e.g., 0.5mm distance, 5mm/s speed).
- Reduce Nozzle Temperature: Lower by 5−10∘C increments until stringing reduces without affecting layer adhesion.
- Dry Your Filament: Use a filament dryer box, a food dehydrator, or even your printer’s heated bed (at a low temperature) to remove moisture.
- Enable “Combing Mode” (if available): This slicer setting can help the nozzle travel over already printed areas to minimize stringing.
Problem 3: Clogged Nozzle
A frustrating but common issue that stops prints in their tracks.
- Symptoms: No filament extruding, under-extrusion, grinding sounds from the extruder.
- Likely Causes:
- Debris in Nozzle: Dust, old filament, or carbonized material.
- Heat Creep: Heat travels up the hotend, causing filament to soften prematurely and jam.
- Retraction Issues: Excessive retraction can pull molten filament into the cold end.
- Dirty Extruder Gear: Filament dust can accumulate, leading to poor grip.
- Solutions:
- Cold Pull (Atomic Pull): Heat the nozzle, push some filament through, then let it cool slightly before pulling it out quickly. This can remove debris.
- Nozzle Cleaning Needle: Carefully insert a fine needle (often included with printers) into the nozzle opening.
- Disassemble and Clean Hotend: For persistent clogs, you may need to partially disassemble the hotend to clear the obstruction.
- Check Extruder Gear: Clean any accumulated filament dust with a brush.
- Ensure Proper Cooling: Verify your hotend fan is functioning correctly to prevent heat creep.
Problem 4: Layer Shifting
When your print looks like it’s been pushed sideways mid-print.
- Symptoms: Layers are misaligned horizontally, creating a “stair-step” effect.
- Likely Causes:
- Loose Belts: Stepper motor belts are not taut enough, causing them to slip.
- Motor or Pulley Issues: Loose pulleys on stepper motors or damaged motor drivers.
- Obstructions: Something physically impeding the print head’s movement.
- Print Speed Too High: The printer’s motors can’t keep up.
- Solutions:
- Tighten Belts: Gently tighten the X and Y-axis belts until they have a slight tension without being overly tight.
- Check Pulleys: Ensure all pulleys on the stepper motors are securely fastened.
- Clear Obstructions: Make sure no cables or debris are in the path of the print head.
- Reduce Print Speed: Especially for complex prints or at higher layer heights.
- Check VREF on Stepper Drivers: (Advanced) Incorrect VREF can lead to motor skipping, but this requires caution and knowledge of electronics.
The Cornerstone of Quality: Routine 3D Printer Maintenance
Prevention is always better than cure. Regular maintenance will save you headaches and extend the life of your printer.
Daily/Before Each Print:
- Clean the Build Plate: Wipe down with IPA or your preferred cleaner.
- Inspect for Debris: Quickly check for any loose filament bits or dust on the printer frame.
- Check Filament Path: Ensure the filament spools freely and isn’t tangled.
Weekly/Every Few Prints:
- Lubricate Z-Axis Rods/Lead Screws: Apply a thin layer of white lithium grease or a specialized dry lubricant to the lead screws. This ensures smooth vertical movement.
- Inspect and Tighten Belts: Check the tension of your X and Y-axis belts. They should be taut but not overly tight.
- Clean Extruder Gear: Use a brush or compressed air to remove any filament dust from the hob gear.
- Inspect Nozzle: Look for any visible wear or damage. Consider replacing if it looks worn.
Monthly/Every 100+ Print Hours:
- Deep Clean Hotend and Extruder: If you’ve had issues, consider a more thorough cleaning or even a hotend “cold pull” to clear any potential internal blockages.
- Check All Screws and Connections: Ensure all frame screws, motor mounts, and electrical connections are secure.
- Inspect Wires and Cables: Look for any fraying or damage. Secure loose cables with zip ties or cable management sleeves.
- Calibrate E-Steps (Extruder Steps per Millimeter): This ensures your printer is extruding the precise amount of filament commanded by the slicer. This is a crucial calibration for dimensional accuracy.
- Check Fan Functionality: Ensure all fans (hotend, part cooling, power supply) are spinning freely and quietly. Dust them off if needed.
Annually/Every 500+ Print Hours:
- Replace Nozzle: Even if it looks fine, nozzles wear down over time, affecting print quality.
- Replace PTFE Tubing (Bowden Systems): PTFE tubing can degrade internally, increasing friction and causing extrusion issues.
- Inspect Bearings and Rods: Check linear bearings for smooth movement and rods for any scoring or wear. Replace if necessary.
- Firmware Update (if available and recommended): New firmware can bring bug fixes, new features, and performance improvements. Always research thoroughly before updating.
Optimization Beyond Maintenance: Slicer Settings and Environment
Beyond the physical health of your printer, your slicer settings and printing environment play a significant role in print quality.
Slicer Settings: Your Digital Toolbox
- Filament Profile: Create and fine-tune specific profiles for each type and brand of filament you use. Different materials require different temperatures, retraction, and cooling.
- Print Speed: While tempting to print fast, slower speeds often lead to better quality and fewer errors, especially for complex geometries.
- Layer Height: Thinner layers (0.1mm−0.2mm) result in smoother prints and finer details but increase print time. Thicker layers (0.28mm−0.32mm) print faster but show more prominent layer lines.
- Infill Density and Pattern: Adjust based on the part’s required strength. For display pieces, 10−20% infill is often sufficient.
- Supports: Use supports judiciously for overhangs that exceed your printer’s bridging capabilities. Experiment with different support types (tree, normal) and densities.
- Initial Layer Settings: Often overlooked, but critical. Slightly slower initial layer speed and increased extrusion can greatly improve bed adhesion.
Environmental Considerations:
- Temperature Stability: Maintain a consistent ambient temperature around your printer. Drafts and sudden temperature changes can lead to warping, especially with ABS.
- Enclosure: For materials like ABS, ASA, and Nylon, an enclosure is highly recommended to maintain a stable, warm environment, preventing warping and improving layer adhesion.
- Humidity Control: Store filament in a dry environment. Use desiccant packets in sealed bags or a dedicated dry box. Wet filament is a primary cause of stringing and poor print quality.
- Cleanliness: Keep your printing area clean and free of dust, which can contaminate filament or enter printer components.
Empowering Your 3D Printing Journey
Troubleshooting and maintenance are integral parts of the 3D printing hobby. By understanding common issues, implementing a routine maintenance schedule, and optimizing your slicer settings, you’ll not only resolve problems quickly but also prevent them from occurring in the first place. This proactive approach will lead to more successful prints, less frustration, and ultimately, a more enjoyable and productive 3D printing experience. Happy printing!
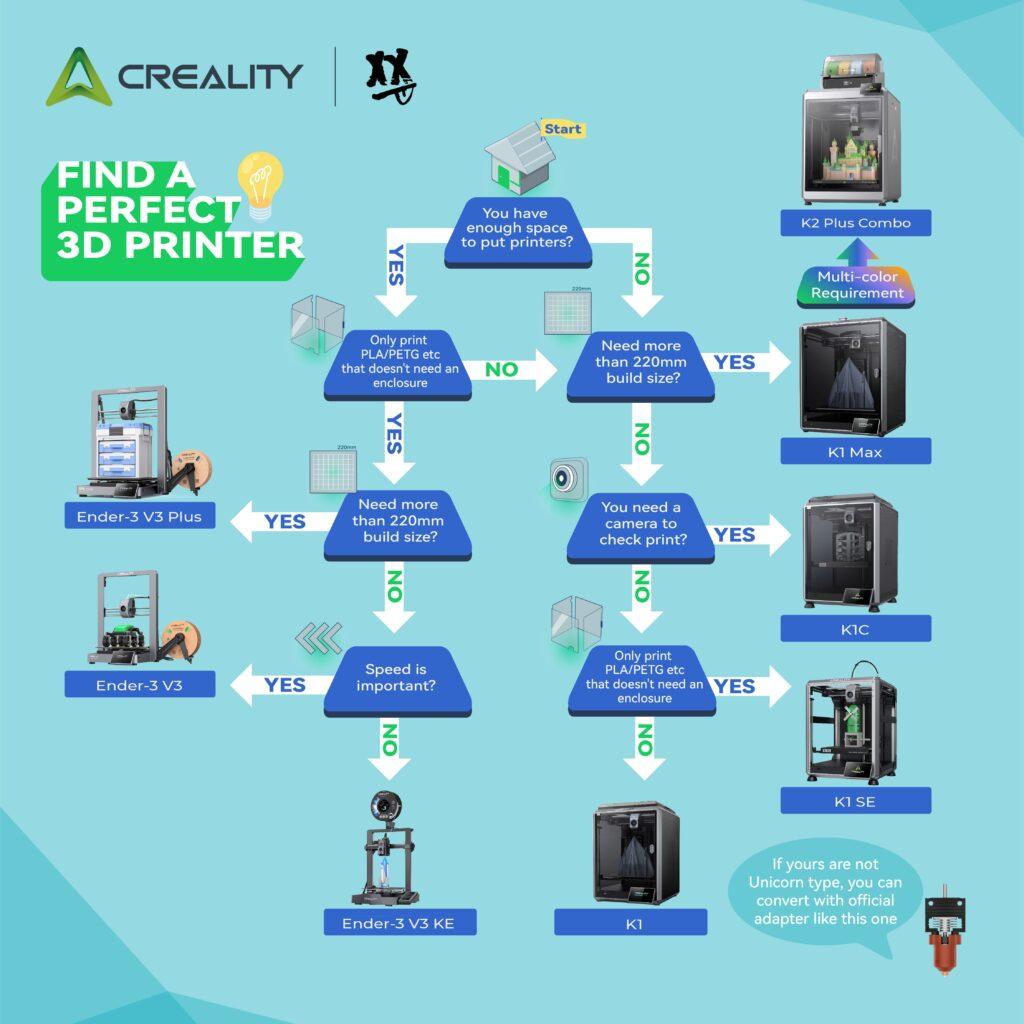